Manufacturing tools required for cutting, stripping and terminating 3-pin cables?
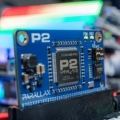
Hey all,
Feel free to send me to Google, but I'm also looking for some input from people who may have experience with this process (like Andrew, WBA).
Parallax sells a tremendous number of these 3-wire "servo extension cables" in 10-in and 13-in sizes. At present these are made in China but we are considering moving the process to Rocklin, California so we have more control over the whole process. We would increase the variety of wire sizes and lengths (up to 2 meters) and assemble the highest quality product possible. The actual stranded wire would likely come from a Taiwanese supplier and would be available in sizes 18-24 AWG with white, red and black wire.
Most of our sensors use this connection style. Here's a picture:

I'd like to identify the right kind of equipment for running this process in high volume (at least 10K cables/month). What kind of stripping machine is required for this type of wire and what's the process like for putting the connectors on the wire? I'm familiar with the low-volume, hand-work approach, but not the automated approach.
I realize it seems totally backwards to consider doing this in the USA if it's not automated. Maybe I should share the reasons I'm even looking at it. First, we have a growing commercial customer base who warrants the best product available. We don't want a sensor-based control system failing because of a low-quality cable. Next, a diverse assortment usually involves lower volume on a per-part basis, making Asian sources a challenge due to high volume requirements, lower inventory turns, and longer lead times.
Any links to suggested wire stripping machinery, termination/connection processes or connector suppliers would be most helpful.
Thanks,
Ken Gracey
Feel free to send me to Google, but I'm also looking for some input from people who may have experience with this process (like Andrew, WBA).
Parallax sells a tremendous number of these 3-wire "servo extension cables" in 10-in and 13-in sizes. At present these are made in China but we are considering moving the process to Rocklin, California so we have more control over the whole process. We would increase the variety of wire sizes and lengths (up to 2 meters) and assemble the highest quality product possible. The actual stranded wire would likely come from a Taiwanese supplier and would be available in sizes 18-24 AWG with white, red and black wire.
Most of our sensors use this connection style. Here's a picture:
I'd like to identify the right kind of equipment for running this process in high volume (at least 10K cables/month). What kind of stripping machine is required for this type of wire and what's the process like for putting the connectors on the wire? I'm familiar with the low-volume, hand-work approach, but not the automated approach.
I realize it seems totally backwards to consider doing this in the USA if it's not automated. Maybe I should share the reasons I'm even looking at it. First, we have a growing commercial customer base who warrants the best product available. We don't want a sensor-based control system failing because of a low-quality cable. Next, a diverse assortment usually involves lower volume on a per-part basis, making Asian sources a challenge due to high volume requirements, lower inventory turns, and longer lead times.
Any links to suggested wire stripping machinery, termination/connection processes or connector suppliers would be most helpful.
Thanks,
Ken Gracey
Comments
Next to Browser and the pair of loaded dice I got for my high school graduation, the Parallax servo extension cables in my shop are my most valued possessions (even ranking above the '82 Benz). So I'm glad to see you planning to ramp up production of these precious commodities.
I know nothing about the equipment required to produce them. But I do know that electronic service bureaus love to brag on their websites about the fancy equipment they own, including make and model numbers. Perhaps Googling cable strip crimp service, or somesuch, will lead you to a bunch of service bureaus whose equipment listings you can derive some clues from.
Good luck with your quest!
-Phil
Hope this helps!
The tool you want takes a strip of these contacts http://www.alliedelec.com/search/productdetail.aspx?SKU=2465574 or similar
I have also tried to find stranded (not solid), mutli-colored ribbon cable in bulk with no luck.
I have a Berg hand tool that doesn't require any wire stripping. The die that's in it right now is intended to crimp a 4-position connector to a flexable circuit similar to the Flex Force sensor we carry and mate it with a connector end equivalent to the servo connector. It's yours if you want it, but it will need a different die for the connection you want. Point is, you may not require any wire stripping, and the hand tool would use the same die as the automated machine so you could test a few manually.... and for 658+ connections per day (assuming you have a connector on both ends) that seems like a pretty light load for an automated crimper.
Beau, could you send me this tool so I could at least get familiar with how it is used? I guess I need to find the right die for it, as well as the 3-pin connectors. Perhaps we could get the process rolling with this approach, just to get our inventory levels up before we switch to a fully automated solution. Half of the work in setup lies in creating an assortment of stock codes and styles. If we're going to enter this arena, we're going to do it entirely correctly: the best wires and connectors, testing every one we produce, and offering them in a far wider selection of sizes. One challenge we'll have is finding a quality, pliable stranded 3-conductor cable - I've seen a lot of Smile (yes) with stiff wires and shielding.
I'll follow up on the supplier leads next.
Thanks,
Ken Gracey
Out of curiosity of what such a machine would look like I did a search and found Artos Engineering. Interesting machines, don't know if they have what your looking for though.
-Ron
A tremendous thank you for the solutions and leads to equipment. Gordon sent me an offline e-mail to a really simple set of parts that Pololu is providing so I've asked him to post that on these forums for others to find. From a high-volume manufacturing perspective I had a nice conversation with Andrew and that provided some insight to the whole process, followed up with some calls to Molex and Schleuninger. A production approach requires a few pieces of equipment and it still includes a few manual steps.
We've located the wire in Taiwan - if you are familiar with our 68-inch cable http://www.parallax.com/StoreSearchResults/tabid/768/List/0/SortField/4/ProductID/612/Default.aspx?txtSearch=68%22+cable then you know the product and quality we'd source. It's a very tactile, soft and flexible cable with a high-quality 22 AWG stranded wire.
This wire is either cut manually and then stripped three at a time with a machine like this one: http://www.schleuniger.com/DesktopDefault.aspx/tabid-46/89_read-831/ or the entire cut to length/stripping operation can be done by a single machine http://www.schleuniger.com/DesktopDefault.aspx/tabid-44/74_read-1590/ . These machines range from $10-25K, before our purchasing manager gets their sales people to concede.
Next you attach reels of the Molex 70058 crimp terminals http://www.molex.com/pdm_docs/ps/PS-70058.pdf into this Molex Universal Crimp Press http://www.molex.com/molex/products/family?key=tm3000&channel=products&chanName=family&pageTitle=Introduction and the metal crimps are attached to each wire, one at a time. This machine is about $7K.
Then, you'll manually press the three crimped conductors into the 1x3 terminal block housing - snap, snap, snap. This step is not automated, at least in the volumes we're looking into.
I think the equipment to do this properly is probably about $20K. I'd have to look carefully into the volume we are consuming, the cost of the raw material, and the opportunity created by being able to offer more lengths of cable (some boring spreadsheet analysis with some variables here and there) to know if this is even worthwhile. One benefit is that the Federal government extended Section 179 benefits so that the whole amount can be written off the first year. I certainly don't look to the government for inspiration, but I have to admit that the Section 179 benefit has been useful in our business in that it provides additional reasons to make a purchase.
More research has to be done. Maybe this post will yield some other ideas we need to consider.
Ken Gracey
Equipment research and purchase takes a lot of time. Every time I look into equipment I go through the same process (like you do). The failures we've had in the past were almost always in used equipment purchases, except for equipment that was already well-understood by somebody in the office. LPKF PCB engravers, Schlumberger E-beam probers and Haas Milling Machines were purchased used with success, but we've made our share of mistakes with reflow ovens that can't bake cookies, granulators that choke on a couple of rails of DIP chips, and pick-n-place machines that require a special visitor from Germany every time the machine needs tweaking. Now I'll only go with mainstream brands and I must be able to talk to other customers who own the same machine.
These forums are a goldmine. Just waiting for somebody to tell me to "go Google it next time". Come on, somebody has to say it!
Ken Gracey
I see the individual wires and Molex shells in addition to 3- (and hopefully 4-pin) premade wire sets.
Anyway, this is what I sent Ken....
Look here:
http://www.pololu.com/catalog/product/1902
at one of several sizes of 0.100" shells Pololu is offering. They have them in various configurations from 1x1 to 2x16. What's better is that they sell pre-crimped wire with male and/or female ends already on them. They come in various lengths and colors:
http://www.pololu.com/catalog/category/71
I've purchased their rainbow sets in 3", 6", and 12" lengths. It's nice being able to make my own cables, using whatever mix-and-match I need -- for example, sometimes I need a 5-pin female on one end, and a 2 male and 3 pin female on the other, going in completely different directions. Maybe this is something Parallax could offer?
Plus they sell the crimp terminals, male or female, if you want to make your own wiring:
http://www.pololu.com/catalog/product/1931
-- Gordon
Thanks for sharing the details, Gordon.
Ken Gracey
Here is Teflon wire manufacturer here in the USA, Vermont,
http://www.phoenixwireinc.com/
They make custom Teflon coated wire/cable, I cant say how many times I have melted the plastic coatings on standard wire. Teflon coated is the answer! The coating is generally thinner, but it is a little more expensive. For quality, it pays off well in my opinion.
EDIT: Also, with my experience with Teflon coated wire is it is more slippery against other Teflon wires, so it may solve the stiffness problem.
Yes it would be nice to have it Made in the USA, but you are aware of the burden of California labor laws. And it certainly is hard to automate. I have the tools to make my own and I do.
the uncrimped connectors.
and the plastic plugs
I will send you back a drawing of a machine. It will be a good exercise in machine design for me.
I work cheap, Pizza, Dr pepper parallax stuff.
Essentially, you are looking for three machines - probably all sit on a work table together.
1. one that repetitively cuts wire to length
2. one that strips both ends to be ready for crimp
3. one that crimps appropriate connectors on the end supplied from a spool of connectors.
The obvious fourth step of inserting into a housing seems to me to be pretty much a manual process, but not an unproductive one.
I've rather grown to dislike ribbon cables as a solution with anything other that specific connectors designed for ribbon cables. They are hard to strip and hard to divide into individual leads. And the wire is rather flimsy for connecting to a crimped connector unless one tins the ends. So a good connection ends up being a rather tedious affair. I've had several servos that I shortened excessively long leads on and they required doing this process several times before I got a good connection.
Besides, you have a lot more versatility with spools of individual wires to use the same machinery for other things. And most importantly, I have found that I can often manipulate a wiring harness (that is NOT a ribbon cable) in ways that are just as good as building a custom circuit board - but a lot cheaper.
These guys will do whatever you want and at any scale you want to do so.
George, I think you are right about the versatility of using individual wires. Some of the hobby wires used for R/C servos are not molded together but spiraled into one wire. This approach certainly provides more freedom when it comes to connectors. But as a finished product it appears a little less "polished".
Looks like I might have found a really good source in Taiwan for this service. I hate the idea of loosing the freedom of being able to make decisions one day and have the product the next. Aren't people supposed to get more patient and wise as they grow older? I think that having lived with a life of long R&D/product development lead times at Parallax I truly appreciate the times when we can simply envision a solution to a need and solve it all within the same week.
Ken Gracey
I am sure these "Automated" machines don't just load themselves... Thanks again. :thumb:
-Tommy
Hey Tommy, you're welcome. There are tremendous values of keeping work like this in the California manufacturing facility. I'll be honest - it's taken me several years to fully understand all of the variables and how they work together (I've only learned as Parallax has grown and didn't have any innate MBA traits to throw at this). Even if you remove the patriotic Made in the USA mantra and the fact that one additional job at Parallax is a valued 2% increase in our employment (we have 50 employees), the other benefits are significant: lower inventory levels and higher turns; higher quality; less administrative overhead; and dramatically faster turnaround times. Many companies focus on the fact that it costs $3 in China and $8 in the USA, but there's more to it than that. We have a Hong Kong and Chinese business specifically for this purpose led by Ari, coupled with a team that's part of our family. Sometimes it's worth sending manufacturing overseas, other times it is not. I'll put this monster project in a spreadsheet and the right answer will emerge.
Even if it isn't fully automated, I'd still consider bringing this process inside the office. People can do automated jobs, and with the variety of equipment at Parallax it's easy to mix up the tedious processes and support the team with different tasks. These positions come with full benefits at Parallax, too.
Nice day in Pismo Beach,
Ken Gracey
OK - this little machine you are designing costs $7,000 on the market, but they are capable of doing many more types of wire stripping (right now we only want to be able to do this single type of wire). I'm not at all opposed to custom tooling, especially when the tool is designed for a process we do in volume. We have tools like this for cutting PCBs, soldering BS2 legs, programming chips, etc.
I'm open to this as an option. We have a local machine shop who can make parts out of stainless if necessary.
Please drop me a message kgracey@parallax.com and I'll send you all the parts you need to build and terminate cables.
Ken Gracey
Pffft! Hardly. Having less less time remaining with each successive day, I think it works the other way -- at least with the patience part.
-Phil
When I first got involved in the microcontrollers, I tried to make a board for everything. Many went in the garbage. But now I make up a wiring harness that can jump from one board to the next AND re-arrange the wires along the way.
If you get involved in buying machinery to make wiring harnesses, it can allow you to easily reconfigure one board or device with another. For example, the Propeller Proto Board in RS232 form has 3 alternative programing ports to accommodate USB to Serial adapters in 2 different configurations. This could have just as easily been provided for by a cable as an adapter. Electronic stores such as Radio Shack are full of cables as adapters. So having the machine handy may in some cases mean that you don't have to worry about the perfect board for all your other items in stock.
The little black connectors from Pololu are the exact same ones I prefer to use as they seem to have superior electrical contact over some others that just make contact with a pin on one side. So it is an excellent form factor to start with. I have black cases for 1, ,2, 3, 4, 5, 6, 8. 10, and 12 wires at home for whenever I think of something.