Milling sheetmetal - fixturing tips?
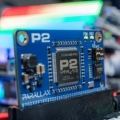
Hey all, the laser cutter and Delrin have been a fantastic choice for my quadcopter, but I'd like to take a whirl at CNC machining some sheetmetal for some airframe chassis parts. Normally sheetmetal is machined on a CNC punch and it's not too practical to mill it due to fixturing issues.
But I know many of you have done this successfully. I suppose the absence of coolant makes it a whole lot easier to secure but results in a poor finish.
The kinds of pieces I'd mill would be 6061 0.063 aluminum, about 7" square or smaller. What kinds of tricks do you have for securing this to the table? Any special double-sided tape? Are you drilling the holes first and then securing with screws into a fixture underneath? I'd really enjoy a hassle-free approach if one exists. Bonus points if the setup can accommodate coolant. No magic please.
Thanks in advance for the tips!
Ken Gracey
But I know many of you have done this successfully. I suppose the absence of coolant makes it a whole lot easier to secure but results in a poor finish.
The kinds of pieces I'd mill would be 6061 0.063 aluminum, about 7" square or smaller. What kinds of tricks do you have for securing this to the table? Any special double-sided tape? Are you drilling the holes first and then securing with screws into a fixture underneath? I'd really enjoy a hassle-free approach if one exists. Bonus points if the setup can accommodate coolant. No magic please.
Thanks in advance for the tips!
Ken Gracey
Comments
The way I do it is to clamp the sheet metal to a sacrificial piece of MDF, as shown in the photo (which shows G10, rather than aluminum):
Don't overtighten the clamps, because the aluminum might bow upwards. You also have to be careful planning the cutting path, since a spiral-flute mill will tend to pull the sheet metal upward, and you don't want it flapping around while it's being cut. (I've sometimes resorted to pressing down on the metal with my fingers while it's being cut to keep it from vibrating -- but you didn't read that here!)
Another method I've used is to clamp the sheet suspended between two metal blocks. I don't have a flood cooling system, though, so it's hard to keep coolant pooled where it's needed, since it runs away through the cut slot.
In any case, vibration and flapping around of an almost-finished piece are the biggest issues. But I've only ever used spiral-flute mills. You might have better luck with a milling cutter having vertical flutes, since it won't tend to pull up on the material.
-Phil
@Phil. OK. I think I could give this a try. The biggest problem is lifting the sheetmetal up off of the MDF as you pointed out. I'm not familiar with vertical-flute cutters, only spiral cutters. That's another good idea to try. Any luck with adhesives of any kind? I realize it's a hassle to clean them off of the metal afterwards, but I'm happy trading that labor for other headaches like making a fixture.
Thanks for the tips so far!
Ken Gracey
-Phil
Ken Gracey
-Phil
Also, depending on what you are cutting out, you could leave little "break away" spots that you can snip out after it's done.
If the design is similar to your other designs with a hole in the center, you could drill a hole in the center first and bolt it to MDF or whatever that might keep it from lifting but then you would have to cut out the center last. Just a thought.
-Ron
-Phil
@Roy, this stuff climbs up end mills something terrible. An inch away from a hold-down of some kind can be too much with 0.050" aluminum. The break-away spots could be useful in combo with Ron's suggestion.
Thanks for sharing the ideas.
Ken Gracey
-Phil
Another thing I've read is that you can stack a few sheets and cut that and only the top one is "throw away".
Didn't think about using 5052 but I'll take a look at the metal properties. As long as it's not too gummy it should work great. Thanks for the tip.
Ken Gracey
-Phil
I would use 6061 it machines the best. Use a carbide 2 flute end mill 1200-2000 rpm at about 2-3 feedrate. Play with the rpm till you see chips coming off not dust. Take about .035 of at the most in one pass. I use these rates with a 3/32 or 1/8 endmill.
Do a rough cut first at the rates above. Cut you piece out about .01 - .015 larger than it should be and then do a 2nd pass at the correct dimension same rates as above but at the whole depth of the material (.063). Then do a final pass at 10-15 in/min at the whole depth of (.063).
Heres a link to my last project. The wings are from .032 and the body is .063
http://forums.trossenrobotics.com/showthread.php?t=4561
Thanks Duke - I think your approach is ideal if I can make it work properly I'll do it. I'm planning ahead to do this project in about 10 days, not a minute sooner because of obligations elsewhere.
Most importantly: WELCOME TO THE FORUMS! The welcome committee would like to make you right at home. We're glad to have you as part of the ongoing, 24/7 action. You'll find lots of qualified people on this forum - I'm more of a learner than a contributor but I have tremendous respect and appreciation for those who can answer the real technical questions.
Ken Gracey
If you have any more questions or anything, feel free to ask. I'm a lead CNC machinist at a full service engineering firm. And once I get my Boe Bot here in a few days, I'm sure I'm going to have tons of questions to get it up and running.
Since you're 10 days out I'll post you a roll tomorrow. I owe you a roll of tape anyways
It would certainly make your efforts more safe and repeatable.
Besides, making chips is fun!