Trace length, when is it important, and when can I ignore it.
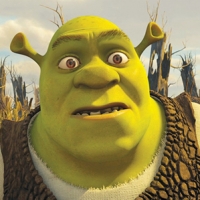
For the last several days I have been trying different trace layouts that lead from the Propeller to a breadboard, and 4 bit lcd. At first I didn't care what my trace lengths they were, but tonight I noticed how easy it is to create lengths greater than a inch longer than the average length of my other traces leading to the bread board.
1) Is it good practice to keep traces from the propeller within a +/- range? or not necessary?
2) I have often read to use decoupling capacitors as close to the chip as possible. I know the trace length is important here, but if I use 2 capacitors, should all the traces be the same length? or is it ok to have longer traces near the crystal (29 & 32) and shorter traces at 9 & 12.
3) I assume the eeprom trace lengths are important.
4) Are the programming trace lengths important?
5) Is there something I else that I should be concerned with.
Thanks
Bill M.
1) Is it good practice to keep traces from the propeller within a +/- range? or not necessary?
2) I have often read to use decoupling capacitors as close to the chip as possible. I know the trace length is important here, but if I use 2 capacitors, should all the traces be the same length? or is it ok to have longer traces near the crystal (29 & 32) and shorter traces at 9 & 12.
3) I assume the eeprom trace lengths are important.
4) Are the programming trace lengths important?
5) Is there something I else that I should be concerned with.
Thanks
Bill M.
Comments
Decoupling capacitor and crystal connection lengths don't need to be equal. I'd keep the crystal tracks < 0.5".
Other connections like the EEPROM and the programming tracks don't matter much, within reason.
In general, trace length can be critical in two areas (I'm sure the Forum Wizards can comment deeply):
1 - when the length of a trace approaches the wavelength (or multiple) of the signal using it as a path
2 - when the trace length poses excessive parasitic capacitance (mainly due to circuit board composition)
I believe Number 2 is the reason that there is great emphasis on placing the crystal close to the uC; less parasitic capacitance to disturb the resultant frequency.
Number 1 comes into play at "high frequencies" (what's that?) where reflections can occur resulting in a loss of power.
I don't know what the actual rise/fall times are from the Prop pins, but this gives you some idea about the importance of layout when dealing with fast logic circuitry. A good understanding of electromagnetism is useful for avoiding pitfalls. For fast signals its common to design logic traces as transmission lines (which is why 4 and 6 layer PCBs are common)
The best practice it to keep all leads as short as possible.
http://www.consultrsr.com/resources/eis/induct5.htm
The board is intended to be a "go-between" for wires or cables connected to a sensor or a system of sensors. I don't like having sensors wires hanging off a bread board, so the sensors are connected directly to the board. So if I need a pull-up resistor, or a circuit, I can use the breadboard as a prototyping area only, and eliminate sensor and lcd connection problems. The ergonomics are important because all my USB and power supplies are on my right hand side.
Since I can't really control breadboard and cable wire lengths, I was hoping I was just making trace lengths overly complicated. Based on your responses, everybody would probably agree that capacitance could be an issue. But will capacitance really make any difference given I have no control over the breadboard or the wires connected to the board? About half of you say "not to worry about it" ---although Beau is making me think twice about how far a hall sensor can be located from the Propeller.
I really don't want to use up a chunk of your time, because I know it would be easy for me to get technical about every little detail. I have posted my current trace routing from the Propeller to the bread board and programmer, so you can give me just a simple answer: Am I screwing up? or it looks like Smile, but it will be OK.
Thanks
Bill Mazzacane