RCTime and PWM?
My program testing RCTime and PWM fails on both. RCTime result is always zero at all settings of the 10K pot. PWM sets both FETs to 3.3 volts instead of pin8 to 3.3 and pin9 to 0. Please tell me what's wrong. Thanks.
Here's my board
so the pins can be verified.
The extra parts are:
RCTime from 10K pot / ,01uf / 220 ohm to pin.
PWM to IRF3708 FETs with 1N4001's to control a valve.
LED's to show state in next program.
Also, is there a way to increase the resolution on PWM from 8 bits to 12 or from 256 to 4096? I saw other PWM programs that use the video circuitry, should I be using one of those? Thanks.
var long us, ms OBJ Debug: "FullDuplexSerial" con _clkmode = xtal1+pll16x 'For Debug _clkfreq = 100_000_000 'For Debug cntMin = 400 ' Minimum waitcnt value to prevent lock-up PUB CodeTest | x Debug.start(31, 30, 0, 115200) waitcnt(clkfreq*3+cnt) 'For Debug Startup dira[15]~~ 'set pin to out repeat dira[13]~~ 'set pin to out outa[13] := 1 ' charge the cap HIGH PAUSE(1) ' for 1 ms x := RCTime(13,1) Debug.Str(string(13,"Test dec: ")) Debug.dec(x) Debug.Str(string(13,"Test hex: ")) Debug.hex(x,1) Debug.Str(string(13,"Test bin: ")) Debug.bin(x,12) Debug.Str(string(10)) outa[15] := 1 PAUSE(1) outa[15] := 0 PWM(8,255,1000) PWM(9,0,1000) PUB RCTIME (Pin,State):Duration | ClkStart, ClkStop {{ Reads RCTime on Pin starting at State, returns discharge time, returns in 1uS units dira[Pin]~~ ' Set as output outa[Pin]:=1 ' Set high Pause(10) ' Allow to charge x := RCTime(Pin,1) ' Measure RCTime DEBUG(x) ' Display }} DIRA[Pin]~ ClkStart := cnt ' Save counter for start time waitpne(State << pin, |< Pin, 0) ' Wait for opposite state to end clkStop := cnt ' Save stop time Duration := (clkStop - ClkStart)/uS ' calculate in 1us resolution PUB PAUSE(Duration) | clkCycles {{ Causes a pause for the duration in mS BS2.Pause(1000) ' 1 second pause }} clkCycles := Duration * ms-2300 #> cntMin ' duration * clk cycles for ms waitcnt( clkCycles + cnt ) ' wait until clk gets there PUB PWM(Pin, Duty, Duration) | htime, ltime, Loop_Dur {{Produces PWM on pin at 0-255 for duration in mS BS2.PWM(5,128,1000) }} PWM_Set(Pin, Duty, 8) Pause(Duration) PWM_Set(Pin, 0, 8) Pub PWM_Set(Pin, Duty, Resolution) | Scale {{Produces constant PWM on the specified pin. Resolution is the bit of resolution desired, for 0 to 2n-1 8, duty is 0 to 255 12, duty is 0 to 4096 etc Repeat x from 0 to 4096 BS2.PWM_Set(2,x,10) ' pin 2, x value, 10-bit BS2.Pause(10) }} if duty == 0 ' freq = 0 turns off square wave ctra := 0 ' Set CTRA/B to 0 dira[pin]~ ' Make pin input else Scale := 2_147_483_647 / (1<< (Resolution-1)) ' Calculate scale ctra[30..26] := %00110 ' Set ctra to DUTY mode ctra[5..0] := pin ' Set ctra's APIN frqa := duty * scale ' Set frqa register dira[pin]~~ ' set direction {{ MIT License included by reference. http://obex.parallax.com/objects/30 }}
Here's my board
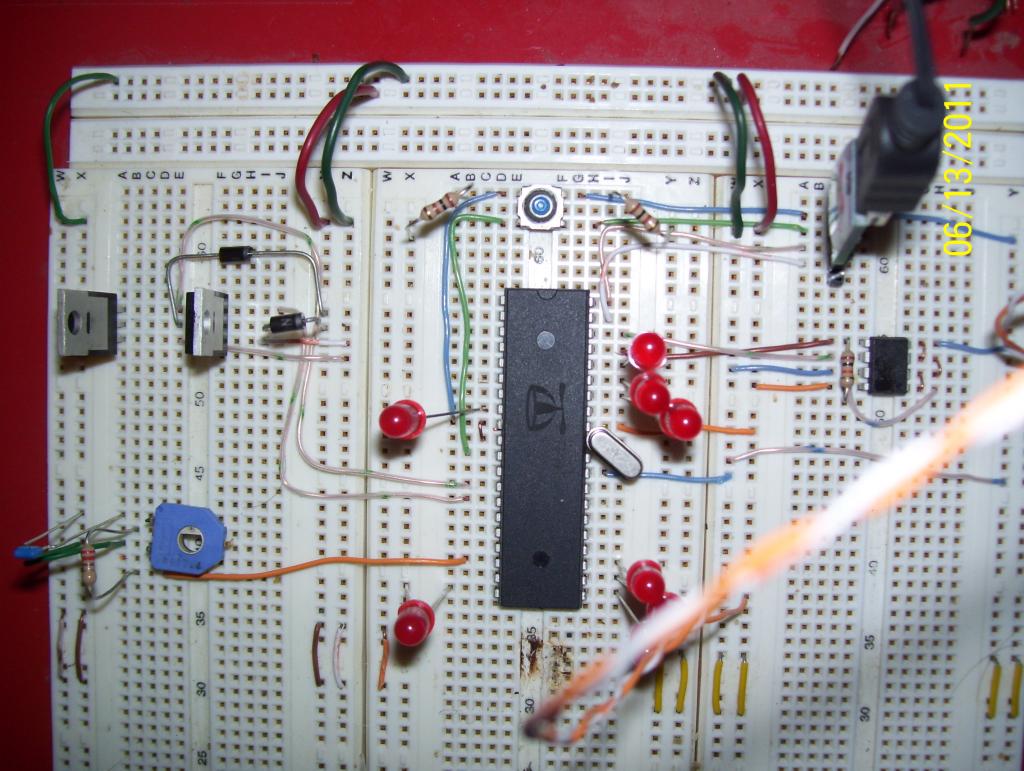
The extra parts are:
RCTime from 10K pot / ,01uf / 220 ohm to pin.
PWM to IRF3708 FETs with 1N4001's to control a valve.
LED's to show state in next program.
Also, is there a way to increase the resolution on PWM from 8 bits to 12 or from 256 to 4096? I saw other PWM programs that use the video circuitry, should I be using one of those? Thanks.
Comments
I'd suggest using the code from the PEK.
I don't see anything connected to the wiper of your POT. Is there supposed to be?
I also notice you're using really thin wire for a breadboard. It looks like the wire inside of phone lines of Cat5 cable? I have a bunch of wire like that myself but I find it doesn't work well in breadboards. I think you ought to try some thicker wire with your circuits.
I haven't use PWM much myself but I think the only factor that would limit the resolution would be the frequency. The higher the frequency you use the less you'll be able to increase the resolution.
Duane
Thanks, I just ordered a PEK book yesterday. The software I copied from the Object Exchange, BS2 functions. I'll look more into the PEK.
The pot wiper has two connectors, the one in the middle of three is connected to a 220 ohm resistor which goes to the prop pin. (It's an unusual pot but it works for position sensing. Many other pots introduce trouble when mounted, with varying resistance due to shaft or resistor plate deformations due to torque or ground problems.)
You are correct, my wire is Cat 5. It did cost me one error on this prototype and probably more. I can get 22 Gauge stranded wire at the local auto shop. Will stranded work?
I can lower the frequency but I'll look into the PEK software first, it may have something to give higher resolution.
Thanks,
Kirk
No, stranded wire will not work. You really need to use solid wire of the correct gauge (22 AWG). If you have a Radio Shack near by, they sell jumper wire in a little plastic box. It is more expensive to buy in the little box than to buy a couple of spools of like the one I linked to but it might be a faster way to get some jumper wire.
Duane
The PEK book in the Prop Tool has nothing searchable on RCTime but there may be enough on time measuring to figure something out with the other code. Fortunately it does have PWM code which works which I should be able to make work for me. Also, I'm thinking there was some demo code I tried which loops to slowly raise the output from 0 to 1 which may also help get the FET to work in a proportional manner, I hope.
Kirk.
Thanks for the RC decay tip.
Absolutely will work. I ahve been doing it this way for quite some time, and have had no problems at all. Just put a thin tin to the ends, so that it is covered, but the strands are still visable. Check out this page for a good couple pictures.
[HTML]
http://store.curiousinventor.com/guides/how_to_solder/prepare/
[/HTML]
The key is uniformity. Make sure it is evenly covered, no icicles, and be carefull of wicking up into the insulation. this can cause more problems. I find doing it this way gives a bit more flex to your work, in case you are like me, and ahve certain "Modules" that are on PCB's that you recycle during development of different projects. Maybe one with a Shift register for quick and dirty IO expansions... one with a RTC and battery (also eliminates problems with XTALs, etc.
The link you provided is for using stranded wire with a circuit board not a breadboard.
It would be nice if one could use stranded wire with breadboards. Standed wire generally flexes better than solid wire. When I looked for information about using stranded wire with breadboards I found this site which says:
Duane
I don't know enough about the BS2 to answer this. Hopefully someone else here does and will.
Then I really don't understand what the BS2 does. I thought that that's what PWM did; control the time on and time off depending on the duty cycle and frequency.
Again, I hope some other forum member can answer your PWM questions.
Duane
"True PWM" is a pulse-width that varies with a constant repetition rate [frequency] (like servo control pulses),
I like pulses coming at regular intervals (clockwork).