Pressure sensors as altimeters: seeking your important customer input!
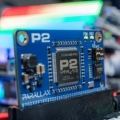
Hey there,
I recently attended a Parallax engineering meeting where one of the topics discussed was pressure sensors. Specifically, sensors that our customers could use as altimeters from sea level to 30,000 feet (or as high as you fly your rockets). Applications might include rocketry, quadcopters, UAVs or telemetry-related projects, or even Parallax Semiconductor application notes.
We're not interested in selling a paintball splattering of sensors and breakout boards to confuse our customers. We want to stock a few of them (maybe from the same family), document their use properly, and support them as well as the company who manufactures them with examples for our microcontrollers. Our value in the sensor business is to help our customers get up and running immediately, with high-quality hardware, and a "Tracy Allen" style scientific approach to calibrate and calculate the raw output into meaningful units. Smart sensors are also welcome, too. Quality and documentation are important in this case.
We would like to hear your suggestions for pressure sensors that we should consider stocking, as components or in a module format. Please tell us in this thread some specific manufacturers of your favorite barometric pressure sensors for the kinds of uses I described above. We'll get them into our inventory.
And most importantly: thank you!
Ken Gracey
I recently attended a Parallax engineering meeting where one of the topics discussed was pressure sensors. Specifically, sensors that our customers could use as altimeters from sea level to 30,000 feet (or as high as you fly your rockets). Applications might include rocketry, quadcopters, UAVs or telemetry-related projects, or even Parallax Semiconductor application notes.
We're not interested in selling a paintball splattering of sensors and breakout boards to confuse our customers. We want to stock a few of them (maybe from the same family), document their use properly, and support them as well as the company who manufactures them with examples for our microcontrollers. Our value in the sensor business is to help our customers get up and running immediately, with high-quality hardware, and a "Tracy Allen" style scientific approach to calibrate and calculate the raw output into meaningful units. Smart sensors are also welcome, too. Quality and documentation are important in this case.
We would like to hear your suggestions for pressure sensors that we should consider stocking, as components or in a module format. Please tell us in this thread some specific manufacturers of your favorite barometric pressure sensors for the kinds of uses I described above. We'll get them into our inventory.
And most importantly: thank you!
Ken Gracey
Comments
Rich H
I have some samples of the HP03M but never did anything with them. IIRC, the price was very reasonable, but they require a bit of external math to do the compensation calcs. 'Nothing the Propeller couldn't handle, though.
-Phil
Here is the list of precalibrated chips and modules, and you see there are absolute sensors for both altitude and depth. I have used the MS5534 and MS5540 and MS5541 with the BASIC Stamp. There is an object for the Prop in the OBEX. It needs a carrier board to adapt it for people who won't want to be troubled with the fussy surface mount package. You could make it really small though to fit into a nose cone. For the Stamp, I had to mount it on a board with a 3V regulator and level translators, and a 32kHz oscillator for its conversion clock. A Prop version could possibly consist of only the chip and a header, although it might be nice not to require the Prop to supply the 32kHz. The interface is standard SPI. The software has to read out the unique calibration constants that are stored in its eeprom and use those in the calculation of temperature and pressure.
Gage pressure is a more difficult for you to stock, maybe because there are so many possible ranges and applications. What application? It seems like questions about engine manifold pressure come up here pretty often. That would be quite a different beast.
On a side note, I would love to see two propeller based products that could utilize this type of sensor: a single board weather station and a rocket telemetry/locator board.
-Phil
Rich H
Ah, so! Something like this, IOW:
I like it!
-Phil
These barometers take quite a bit of electronic filtering before their precision approaches their resolution.
Also see; http://en.wikipedia.org/wiki/Variometer
Rich H
With the MS5540, I've done a program that graphs the immediate value against a filtered value, and that easily shows crossing lines as the barometer moves up and down. Beep boop beep boop? Like Phil's circuit diagram. The MS5540 conversion time is 35ms, so a 64 point average is only 2.25 seconds. Is that a reasonable response time? The new ms5803 is faster and also higher resolution.
The site ballvarios.com seems to be real estate?
I'm confident that the Ball vario does not use a calibrated leak as a method to detect lift but it makes sense that it would be easier to make an accurate vario using a differential pressure sensor that is very sensitive over a small range rather than pulling out the tiny changes in a sensor that measure from sea level to 50,000 feet.
My main point though is that the hose connection is very useful. Even if you were to make a vario with an absolute sensor you will get better results if you can place the static port in the best location AND these days you need to have a total energy probe anyhow which is basically a pitot tube - which necessitates a hose connection on the pressure sensor.
If there is no way to connect tubing to the pressure sensor, then the usefulness of said sensor will be greatly reduced.
Rich H
Jim
The new generation of absolute pressure transducers use 24 bit sigma-delta converters and achieve 0.01 mb resolution (=10cm alititude), and that is over the full pressure range of 10 mb to 1100 mb. Those do not cost any more than the previous generation of 14 or 16 bit converters.
It would not make sense IMO for Parallax to offer a differential (gage pressure) transducer, because there are so many different possible applications with different range and physical requirements. As to the tubing attachment, if it is an absolute pressure sensor, you mount it in the sealed box with a nipple of your choice and run the tubing from that. Granted, there is still the issue of absolute accuracy. .
The resolution at 24 bits is by no means equivalent to accuracy. The accuracy for run of the mill ($ to $$) transducers with basic temperature and linearity corrections comes out at the 1 to 2 mb level. Their high resolution is useful over a short term, such as you would need for a variometer or for a rocket flight. It becomes less useful over longer time periods as you'd need in a precision barometer or depth sensor. Government-type weather stations typically use something like the Setra 278, with an accuracy of 0.5mb at 20°C, and a precision (repeatability and long tern stability) less than 0.1mb, and NIST traceable calibration. That extra accuracy and precision and calibration is what costs $$$. I think ~1mb is fine for a home weather station, especially if calibrated against a local reliable source.
Sure, you could build a box but it would be much larger and less reliable than just using transducers that have the nipples. There is no downside to using transducers that have the nipples that I can see except for the few extra cents that it may cost. The advantage is substantial though. I can see many more demos and app notes for the nipple equipped transducers than those without nipples. But hey, if Parallax decides not to use nipples then someone like myself can offer a module that does use the nipple.
Nipple, nipple nipple.
Rich H
On the flip side, it can be kind of hard to reliably add them.
It appears that the M19 uses an absolute transducer. Is a GPS good enough to derive the velocity component for total energy?
GPS only reports groundspeed. Airspeed rarely equals groundspeed. Even if it did we would want Indicated airspeed and not true airspeed - although I guess true airspeed could be used after compensated for altitude in software. The point is you want to know your velocity through the airmass, not relative to the ground. With a slow flying craft such as a paraglider, GPS speed can easily show you traveling the opposite direction.
When you combine airspeed with GPS data you can calculate windspeed and direction - which is certainly very useful.
Rich H
I think a standard pressure sensor with a pitot (airspeed) and some math will accomplish the same thing when used with the altitude sensor.
Rich H
Jim
Personally, I think a single pressure sensor without a density altitude capability can be done by anybody.
However, I like ideas about stall protection, tip stall measurements, and even for monitoring turbulators for main wings stall & STOL capabilities. But not for air speed, with or without a Pitot tube, or for that matter, anything that requires a hose connection that can compromise a minimal footprint and weight.
However a miniature Density Altitude Weather station with additional data logging outputs in torr, relative humidity, and temp in centigrade will have more applications then I care to list.
Bill M.
Maybe a few, regarding your possibilities. Speed is greatly influenced by temp, humidity and regions of upper atmosphere hi pressure. On the other hand, this also causes serious loss of horsepower for any internal combustion engine powered vehicle. It also as has large implications on propeller choice of any airworthy or boating application, and gearing to compensate for lost horse power of any internal combustion engine on the ground.
Any spark, or compression engines will require different fuel air requirements depending on the time of day, or the local area of operation. Gearing or propeller choice will greatly influences the severity of these changes. Personally I think it is very easy to understand a propeller's pitch/rpm. But not the implications of a propeller choice with regards to the power-plant and all weather operation.
Any spark, or compression ignition engine can easily loose 40 to 50 psi of compression between morning and afternoon in the south-west United States. Similar, but not as severe everywhere else, and least along coastline. If you are not aware of these possibilities, it will lead to problems. My home town is about 1000' above sea level, but density altitude will reach 4500' to 5500' on a hot day.
Data acquisition at home, air, land and sea vehicles, engine management, bicycles, and even for athletes.
Any pro to a hobbyist will find more possibilities than I can list.
Bill M.
(This is my weather station, it costs more than $400.00)
Hope that helps,
Dave
Thank you to everybody who provided us feedback on the request. We've ordered some samples of the Measurement Specialties sensors and will give them an evaluation before we design a couple of modules.
Ken Gracey