HB-25 Assistance Needed
HB 25 Control Problem.
I connected the Propeller to the Motor Mount and Wheel Kit #27971 controller and two HB-25s (#29144).. The controller worked fine. But did not provide fine enough control of motor speed, nor speed reduction.
I decided to control the motors directly just using the HB-25s. I disconnected the cable from the HB-25 to the motor controller and connected it directly to the Propeller. Cable black to gnd and cable white to an output pin through a 1K resistor.
Then I applier a 1.9 ms pulse every 16 ms to each motor. Nothing? I checked the cables, wiring and using an OScope verified the pulse was being sent.
The J jumper is in place at each motor. I know the motors and HB-25s work correctly and they worked when I used the wheel kit controller as an input.
Each motor is fed with +12 volts and the green indicator lights up. I have played with this for three days now and cannot get the motors to turn.
Any suggestions would be appreciated.
I connected the Propeller to the Motor Mount and Wheel Kit #27971 controller and two HB-25s (#29144).. The controller worked fine. But did not provide fine enough control of motor speed, nor speed reduction.
I decided to control the motors directly just using the HB-25s. I disconnected the cable from the HB-25 to the motor controller and connected it directly to the Propeller. Cable black to gnd and cable white to an output pin through a 1K resistor.
Then I applier a 1.9 ms pulse every 16 ms to each motor. Nothing? I checked the cables, wiring and using an OScope verified the pulse was being sent.
The J jumper is in place at each motor. I know the motors and HB-25s work correctly and they worked when I used the wheel kit controller as an input.
Each motor is fed with +12 volts and the green indicator lights up. I have played with this for three days now and cannot get the motors to turn.
Any suggestions would be appreciated.
spin
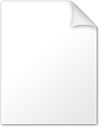
813B
Comments
Rich H
Rich H (W9GFO) provided a clue, saying the HB-25s are sensitive to power up sequence. My experience was that you MUST power up the HB-25 before powering up the Propeller.
However, regardless of sequence, I had to use a driver transistor (2N222A) to cause the HB-25 to recognize commands (pulses) from the Propeller. I believe this is due to the 3.3V Propeller and the 5 volt HB-25?
It would be nice if both of these “features” were noted in the HB-25’s manual.
Larry Cardo
Mentor, OH
Output from Propeller to 1K ohm resistor to transistor base. Emitter to gnd. Collector to 1K res to +5. Collector to white wire on HB-25.
Rich H
No, I don't think that is exactly right. I think what was being said was not to turn them both (propeller and HB-25's) on at exactly the same time. It may be that the propeller pins were temporarily in an unknown state at the same instance as the HB-25's were being power up. I seem to recall coming across a post where someone recommended a pull-up or pull-down resistor on the line to help keep it in a know state while things were being powered up. Controlling them via R/C signals is completely different than using the position controllers. Are you trying to hang both HB-25's off a single line or do you have a separate propeller I/O to each HB-25?
I've been using the position controllers but even without them you don't have to power up the HB-25's first. Actually I prefer (and think it's best) to power them up afterwards when the propeller is up. I'm using the Propeller to control a couple relays that can do power management and one is for the drive system. When the drive isn't used it can be powered off to save energy.
On the robot I have now the position controllers come up with the propeller but I keep the HB-25's off. Those are only turned on after the position controllers (have been setup). I feel this is an absolute must do because of the design of the position controllers. Usually one is setup for reversed orientation. Until that setting has been send to the controller the robot using the wheel kit really isn't safe if the HB-25's and everything is powered. The reason is that if you bump the reversed wheel it will take off running at full speed since the controller is trying to move it back but doesn't know it's reversed since it hasn't been told yet. This one particular setting should have a jumper to hard set the initial setting on the reversed controller so it will be in a safe state without being setup by a host controller first. I've mentioned it before and would like to see that fixed in the next revision of the position cotrollers. It would only take a trivial firmware change (1 line of code in the init) and for the reversed controller tying an unused pin to ground or add a spot w/pullup so a jumper could ground the pin. That way the orientation can be set to the state of that pin during the init. It would be completely backward compatible with existing boards too.
Other than the startup issue on the position controllers they seem to work well. If those aren't doing what you want the Firmware is available for those and they could be tweaked to work the way you'd like.
How is the 2n2222 connected? When I first read that part I would expect that would invert the signal you are sending to the HB-25's and change what you think you're sending to it.
Robert