My Current Prop Based CNC - Photos

Hello Everyone
I finally got around to taking some photos of my current project. It consists of two CNC machines.
Additionally, some of the photos did not upload, so I may delete some and upload others. Please be patient, and eventually I will have some nice photos here. In the near future, I will also make a video of the machines in action.
The wire bending CNC is ready for production, and it will bend 10,800 wire forms in a 24 hour period. It was averaging 12,000, but I had to cut back on the speed due to inaccuracies.
The packaging CNC needs about another weeks worth of work.
Bruce
EDIT: The machine now bends over 25,000 wire forms per day.
EDIT: The packaging machine is currently on hold
EDIT: For those that may be interested, I have attached a PDF to show what the wire bending CNC produces.
I finally got around to taking some photos of my current project. It consists of two CNC machines.
- Wire Bending CNC
- Packaging CNC
Additionally, some of the photos did not upload, so I may delete some and upload others. Please be patient, and eventually I will have some nice photos here. In the near future, I will also make a video of the machines in action.
The wire bending CNC is ready for production, and it will bend 10,800 wire forms in a 24 hour period. It was averaging 12,000, but I had to cut back on the speed due to inaccuracies.
The packaging CNC needs about another weeks worth of work.
Bruce
EDIT: The machine now bends over 25,000 wire forms per day.
EDIT: The packaging machine is currently on hold
EDIT: For those that may be interested, I have attached a PDF to show what the wire bending CNC produces.
pdf
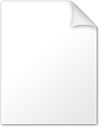
527K
Comments
Graham
A picture is worth a thousand words, except when it comes to motion control, a picture leads to a thousand questions :-)
Chris
@ElectricAye - Funny you should mention that! Several years ago, I had the machine mounted to a wooden cabinet, and there was a laundry basket underneath to catch the packaging. Someone said, "Neat looking machine. Does it fold your laundry?" I have posted that photo below to show how the machine has changed and why that question was raised. It is funny that laundry is always associated with it somehow.
@Graham Stabler - The pictures just don't capture the essence of the machine. I just wish I had better lighting and more room around the machine to take better photos. Anyhow, I probably won't do a video until I get the packaging machine complete. But I will have a video soon.
@Chris_D - There are 16 lighted pushbutton switches that make up a multi-function keyboard and a 2X20 backlit LCD for the monitor. The main programming is of course loaded into each Propeller, however, clock setup, machine setup, production setup, and the production run are all programmed with those 16 buttons. There are six different production sizes to choose from. Wire is threaded from the back spool through the wire straightners (the wire has a curvature which must be straightened) and through the cutting head. The bending head is situated below the plane of the wire, as the machine is running, the bending head raises and makes either a CW or CCW bend, sometimes there there are several bends without lowering the bending head. When all bending operations are complete, the wire is cut, and the wireform is pushed off the table, utilizing a stepper motor, a rack gear, and a Parallax servo. The wireform then slides down that brass tube and into the packaging. When the proper quantity has been achieved, the package is closed and flipped from the working area.
I have to get out more!
Graham
p.s. I covered the roof of my garage in strip lights for reasons of light, works well. If I owned the place I'd also paint the ceiling/walls white.
Yea there are a lot of cool bending machines on YouTube! Some of those machines are really flying. If I had the money, I would have liked to build it with servos for more speed, but I think I will go with pneumatic cylinders for version two. I should have gone that way in the first place, I think it would have been done a long time ago, it would be much faster, and I think I could have done it for a fraction of the price. One of those live and learn things.
However, I must say the bending head on this machine zips around pretty fast
Bruce
May I ask what it is actually making?
Graham
'
Nice machines. I really like all the aluminum in their construction.
'
Is the wire Spring Steel?
That is interesting. I see there are no labels on the buttons so I am assuming that location of the button causes some sort of event relative to the length of the wire?
Chris
@Invent-O-Doc - And thank you for the nice comment.
@Chris_D - The buttons do in fact have labels, but you just can't see them due to my photography
And
A forum member dropped by yesterday just to shoot the breeze and check out my efforts. He curiously asked, "Is that a car part?"
The answer to that question is an emphatic YES! That is 350 Chevrolet flywheel being utilized to turn the wire spool. Additionally, a starter gear was removed from a 350 Chevy starter and was machined to adapt to a NEMA 23 stepper motor to turn the flywheel.
'
My BS2 brush hog uses flywheels and Bendix gears to help get the gear reduction needed for the big flotation tires.
'
153 teeth and 7 teeth and a little grease.
'
Can't wait to see the video!
Bruce
- I abandoned the automatic packaging temporarily due to R&D time constraints, and made a bolt on attachment for the front of the wire bending CNC for manual packaging.
- Since my last post in this thread, I have been working on machine speed and timing issues. I am proud to say that I can now bend one of my special springs every 5 seconds, that's over 17,000 units a day. However, my goal is 20,000, and I believe I can achieve it.
- I still have not made a video, but I will.
Cheers BruceThanks for the update.
I know your goal is 20k/day, but 17k/day sounds impressive to me.
C.W.
- Back in February the machine was averaging 10,800 springs per day. 10,800 * 0.25 = $2700 of product.
- The machine currently averages 17,200 springs per day. 17,200 * 0.25 = $4300 of product.
- As for the goal of 20,000 springs per day. 20,000 per day. 20,000 * 0.25 = $5000 of product.
I anticipate and am hoping that the demand for my product will be higher than I can produce, so the faster the machine goes, the more money I could possibly make. Of course these figures do not include the cost of marketing, materials, packaging, labor, etc... Which of course must all be subtracted from gross sales.Thanks for your interest C.W.
Bruce
I was wrong about my last projections. It looks as though the machine is going to settle in by producing one unit every 5.5 seconds (15,709 per day).
Or do you have to wait for patent stuff?
After a couple days, seems you'd have enought to stock Lowes
Hey there prof_braino what's happening? Long time no see. The machine has changed quite a bit since you seen it, because I have done quite a few modifications for packaging and to make it faster.
I have not started selling yet, however I do have the materials and packaging for 2,000 packages of 20. I still have very little tweaking to do and then I am going to set up an appointment to talk with SCORE (Service Corps of Retired Executives), and see if they have any advice about marketing my product. I also have to get a business phone, etc... before I start selling. But it won't be long now. However a little more investment capital sure would come in handy.
How is your projects coming?
Bruce
Very nice machine! I'd also be interested in a video. But don't say stepper motors are slow. Watch this videos:
http://benezan-electronics.de/forum/videos/Demo-macro.AVI
http://benezan-electronics.de/forum/videos/Demo-micro.AVI
This is a NEMA34 stepper motor driving a 30mm pitch ballscrew. As you can see in the second video with the dial indicator the motion is very smooth in spite of the coarse screw pitch. BTW the current version of my stepper drivers also have a propeller inside.
Bruce
MASSIVE FRUSTRATION
Bruce
Failing that, you could also check out http://DumpsterCNC.com to see if they make (or can make) an anti-backlash nut that's compatible with your lead screw. They're cheap, and the backlash is very low.
I am currently trying a double nut setup with a shim. I just need to shave a little more off one of the nuts and I should have it. Of course this setup will wear the threads quickly, but all the parts came from a couple $5 clamps. Eventually I will change it for one of those Haydon Kerk NEMA 17 linear stepper actuators.
And funny you should mention dumpstercnc, I was just there this afternoon, nosing around a little.
But hey, thanks for the tip and the interest.
Bruce
I have not researched a comparison based upon the coeffiency of friction between HDPE and UHMWPE, but I know they are both pretty slippery stuff.
Bruce