ROV Piston Ballast Tank Motor Postion and Speed Controller
I am building a piston ballast diving tank for a radio control submarine.The piston ballast tank consists of a stainless steel cylinder , a shallow aluminum piston with an outer edge o-ring and aluminum bulkheads for each end of the cylinder.The threaded piston motion shaft is driven by a 6-12 volt brush-less motor having a hollow female threaded motor shaft for moving the threaded piston motion shaft.The motor has a Timken motor encoder mounted on the back of the motor bell housing.The motor is custom fabricated with the motor shaft extended through the motor encoder for sensing position and speed.The motor will operate at a constant speed.I am wanting to buy a motor controller to interface with the Timken motor controller and operate the motor proportionally to enable the submarine to statically dive at different depths.
Someone please help me engineer this electronic controller.
Regards,
John
Someone please help me engineer this electronic controller.
Regards,
John
pdf
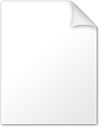
208K
Comments
Left Hanging more than a day or two, this place used to be a little snappier....
The motor controller (ESC) and the motor encoder, are two different things,
the ESC is not controlled by the Encoder, it's controlled by the Microcontroller/Processer/computor.
the encoder just sends the speed and direction of said motor to the Microcontroller, hopefully a Propeller. :smilewinkgrin:
the Microcontroller then takes the encoder info, compass heading, GPS info, Pressure sensors,
Water Temperature, and with the right Probe, the salinity of the water..
all of that data is used by the Microcontroller to Move Your boat around as You wish.
I am not seeing the "hollow female threaded motor shaft " on the motor PDF, You posted.
could You put up a picture? would love to see it...
Again, welcome to the forums, and please realize, Your not being ignored,
Just missunderstood...Happens all the time around here.
Thank you.
The only thing that the brush-less motor with the encoder is moving is the threaded piston shaft.The motor shaft is bored out and threaded to 1/4" to allow the threaded piston shaft movement.The large brass spur gear on the piston motion shaft next to the cylinder bulkhead is where the brush-less motor will be mounted.
Here is a drawing of a similar piston tank but is brushed motor driven with a gear reduction and micro switches for limiting piston travel.I am wanting the encoder to connect to a micro controller to control piston travel and position memory.
Regards,
John
Picture #3 tells the tale really well, I see the "hollow female threaded shaft" now.
Cool stuff...
Some questions for You..
what type of experience do You have with MicroControllers?
any Programming experience? (none required)
What will Your "UnderWaterBoat" do?
Will it send back data from the depths?
What Parts do You have?? (many required)
Just the motor and encoder?
Do You have the Tmax allready? or this is what You want to build?
I ask all this because it could make a difference in the choice of MicroControllers..(Basic Stamps vs Propellers)
Tell Us more about Yer "UnderWaterBoat."
P.S, For future reference, no need to cut and paste the entire post as a quote..Just pick out the good parts...
what type of experience do You have with MicroControllers?
any Programming experience? (none required)
I can program electronic controls for my solar business but have not ventured into this yet.
What will Your "UnderWaterBoat" do?
Will it send back data from the depths?
I will be using it to survey swimming pools with an digital camera at depths of up to 20ft.
What Parts do You have?? (many required)
I only have the 316L stainless steel piston cylinder.
I have been looking and asking questions at Pololu Forum but the techs there treat me like I am from Mars!LOL! I am designing an RC sailboat winch with their JRK Micro controller and is easy to program according to what I read.
I sail an Infinity-54 sailboat that has an obsolete ProBar winch and I'm updating that design.
Just the motor and encoder?
The threaded hollow shaft motor is being custom made by AstroFlight but have not purchased an encoder yet.The motor will be centered over the piston motion shaft.The motor will be mounted where the large brass spur gear is located on the piston motion shaft(T-Max image).This allows the piston ballast tank cylinder to be stacked onto the polycarbonate tubes housing the electronics,sevos and prop motor.Attached WTC image is a similar design.My WTC will have the piston cylinder in the mid-section and have the same size outside diameter as the polycarbonate tubes on each end of cylinder.The bulkheads on each end of the WTC will be aluminum bayonet design for better sealing and for accessing the equipment.
Do You have the Tmax already? or this is what You want to build?
I am custom fabricating the ballast piston tank,bulkheads,piston,motion shaft,etc.It will streamline and update the T-Max design.
I ask all this because it could make a difference in the choice of Micro-Controllers..(Basic Stamps vs Propellers)
I am open to your advice.
Tell Us more about Yer "UnderWaterBoat."
The ROV will be 54" length and 10-1/4" beam.
The propulsion system consists of a single brush-less 1600kv 6.6volt Hall's senser motor.
It uses a programmable ESC.It also has a rudder servo and an elevator servo.The RC radio is a Robbe F-14 Nautical on a 75mHz frequency dual conversion.
Hope I'm not pasting to much.
Regards,
John
:yeah: !!FREE SHIPPING WEEKEND!! :yeah:
Get Yourself a brand new Propeller Proto board, Power supply, and all the other Toys You can afford.
Toy's like the GPS, Gyroscopes, Accelerometers, 74HC595, 74HC165, ect, ect...
Consider the USB version of the Proto Board, it does not require the Prop Clip.
You would only need the Power Supply, and USB Cable.
Look over the Product's, You will find example code for nearly every thing. Alot of it is for the Basic Stamps,
but there are many examples of Spin Code to download also.
If the code is not right with the Product, then head on over to the OBEX, and get what You need.
Between Your Fancy Blue Typewriter ink, and Your well selected Quote's.
Looks to Me, You would have no problem with the Spin Language, it is a very colorfull language.:smilewinkgrin:
check it out and tell Us what You think...
I bet You find the Propeller more usefull and easier then the MicroController You mentioned..
I'm considering this pitch control stamp.
I'm also considering this linear servo for rudder/elevator.
Regards,
John
http://www.youtube.com/watch?v=GymNoaF6zsk
LR-2 Pitch Control Stamp
That's what we call our newest pitch controller manufactured by Model Uboat Specialties. At 30x21x8mm it has the dimension of a postage stamp yet has full pitch control capability with built in SMD technology. It will stabilise submarine models of all sizes. The sensitivity is adjustable smoothly over a wide range. The horizon will be set by appropriate mounting and adjusted from the transmitter.
The sensor detects the movement of hot air in a small cavity via a silicon chip. This sensor is wearless, high precission, and extremly robust. The software allows virtually stepless servo movements even at high sensitivity setting. You can not distinguish it from an analog controller.
Dimensions: 30x21x8mm
Voltage: safe 3.5 - 8.0V, possible 2.0 - 12V