Shadow Bot 2

Shadow Bot elbow test with 100 vdc motor controlled by hacked servo and BS2.
Note the back lash on this elbow test. (24 vdc battery power supply)
No change when run at 36 vdc.
This appears to be a motor, not a relay problem.
When this same BS2 setup is used to run the shoulder motor, it works perfect.
I hate to do it, but may have to abandon the 100 volt motor and go with a heavier 12 volt one.
Any other ideas?
Gramps
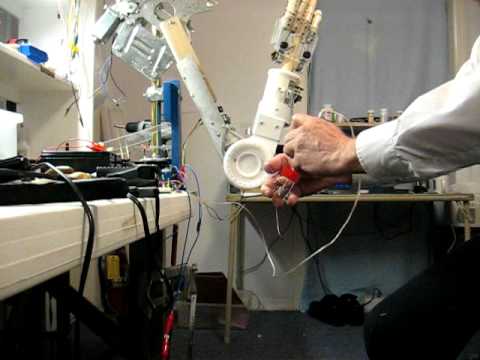
▔▔▔▔▔▔▔▔▔▔▔▔▔▔▔▔▔▔▔▔▔▔▔▔
'What is your life?"
"It is even a vapor that appears for a
little time and then vanishes away."
Saint James 61 A.D.
Note the back lash on this elbow test. (24 vdc battery power supply)
No change when run at 36 vdc.
This appears to be a motor, not a relay problem.
When this same BS2 setup is used to run the shoulder motor, it works perfect.
I hate to do it, but may have to abandon the 100 volt motor and go with a heavier 12 volt one.
Any other ideas?
Gramps
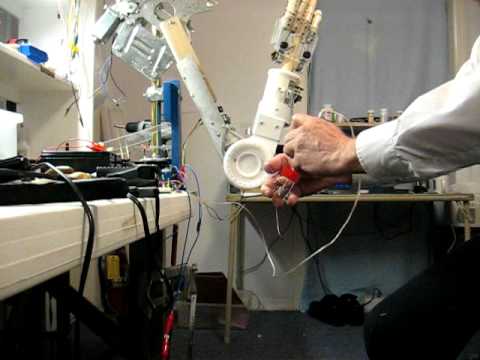
▔▔▔▔▔▔▔▔▔▔▔▔▔▔▔▔▔▔▔▔▔▔▔▔
'What is your life?"
"It is even a vapor that appears for a
little time and then vanishes away."
Saint James 61 A.D.
Comments
▔▔▔▔▔▔▔▔▔▔▔▔▔▔▔▔▔▔▔▔▔▔▔▔
·"If you build it, they will come."
I'd be interested to see what a torsion spring would do in reducing backlash. McMaster-Carr has a big selection of them fairly cheap. You could use an cheap hardware spring on fishing line to test the idea and maybe get an idea how strong a torsion spring you'd need. Harbor Freight has a box of like 300 assorted springs for a couple dollars. That might be a good place to start too.
I don't know how your arm is built, but it seems like a worm gear would be your best bet for gear ratio and reduced/eliminate backlash. Worm gears are generally very strong. Stock Drive Products: http://www.sdp-si.com/web/html/products.htm has a very nice selection of nylon, steel, SS, brass and other open gearing products. They are a little expensive, but if you buy one of something I suppose it's not that bad. Quality Bearings and Components has a lot of open gearing cheap.... but it's typically very robust stuff.....
I'm just giving thoughts. I'm not an expert on this one. My robotic arm isn't NEAR this nice!
▔▔▔▔▔▔▔▔▔▔▔▔▔▔▔▔▔▔▔▔▔▔▔▔
"puff"...... Smile, there went another one.
Post Edited (Spiral_72) : 7/26/2010 8:35:43 PM GMT
We have two counter springs on it to help lift against gravity, but the
voltage is so low for this motor we're not getting the torque it can
supply at higher voltage.
Been experimenting with counter springs but doesn't seem to help much.
A torsion spring might help, i'll look into that........
Tanks for your input!
Gramps
▔▔▔▔▔▔▔▔▔▔▔▔▔▔▔▔▔▔▔▔▔▔▔▔
'What is your life?"
"It is even a vapor that appears for a
little time and then vanishes away."
Saint James 61 A.D.
Wow, no kidding? Is the worm moving when you stop??? It could be you need to shim it or use thrust bearings either side of the worm..... or a steel machined worm and the previous two mentioned things. It MAY not be backlash, but rather the worm/motor shaft moving under stress.
If you tie fishing line (or whatever) to the shoulder.... tied to a spring.... then tied to the wrist, it should do the same thing as a torsion spring would do.... although it'd only be functional at a small degree of motion. A better idea might be tie fishing line to the wrist and throw it over the shoulder with a weight (maybe 6oz?). THAT would better simulate a torsion spring. At least let you know if you're on the right track.
▔▔▔▔▔▔▔▔▔▔▔▔▔▔▔▔▔▔▔▔▔▔▔▔
"puff"...... Smile, there went another one.
The worm gear is actually turning the motor backwards under load
even with the H-bridge config.
Sigh...........
Gramps
▔▔▔▔▔▔▔▔▔▔▔▔▔▔▔▔▔▔▔▔▔▔▔▔
'What is your life?"
"It is even a vapor that appears for a
little time and then vanishes away."
Saint James 61 A.D.
One·drawback of·the humanoid arm layout is that the elbow joint has a horizontal axis, directly affected by gravity. If it had a vertical axis·(as in·the toy Armatron shown), gravity would have negligible effect. This toy's horizontal axis is further out near the wrist, which reduces the load due to gravity.
▔▔▔▔▔▔▔▔▔▔▔▔▔▔▔▔▔▔▔▔▔▔▔▔
·"If you build it, they will come."
hefty to handle a heaver elbow motor.
Tightened up two places where there was just a little slop and it did
make a huge difference in overall operation.
Question: Do the diodes on the relays in the H-bridge protect the contacts from
back emf?
Gramps
▔▔▔▔▔▔▔▔▔▔▔▔▔▔▔▔▔▔▔▔▔▔▔▔
'What is your life?"
"It is even a vapor that appears for a
little time and then vanishes away."
Saint James 61 A.D.
Post Edited (Gramps) : 7/27/2010 1:54:39 PM GMT