Over current problems
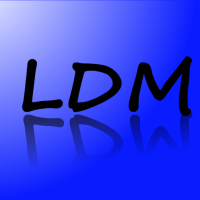
I have a 12V unipolar that I believe is rated for 400ma. I've tried to limit the current from a lead acid battery with 1) a high wattage resistor and 2) a 12V regulator. Both methods waste current. I·switched from a ULN2803 to transistors which improved motor speed but since I'm using a 6V alkaline battery pack the torque suffers. I'm experimenting with mosfets to recover that last 0.6V.
· I'm thinking I could control current with PWM but I can't find a good explanation of what I want to do. I'd like to see schematics for chopper circuits or something. Can anyone point me to a book or other source of information?
▔▔▔▔▔▔▔▔▔▔▔▔▔▔▔▔▔▔▔▔▔▔▔▔
· I'm thinking I could control current with PWM but I can't find a good explanation of what I want to do. I'd like to see schematics for chopper circuits or something. Can anyone point me to a book or other source of information?
▔▔▔▔▔▔▔▔▔▔▔▔▔▔▔▔▔▔▔▔▔▔▔▔
Comments
I have four TIP120s directly driven by a BasicStamp and they allow 5 amps and up to 60 volts. They can also be used for PWM speed control.
From the Basic Stamp, I have a 470 ohm resister to protect the Basic Stamp from excessive current. and there is a 4.7K pull down from the base to ground. Of course, the same could be used to drive a stepper motor and expanded to eight units.
▔▔▔▔▔▔▔▔▔▔▔▔▔▔▔▔▔▔▔▔▔▔▔▔
Ain't gadetry a wonderful thing?
aka G. Herzog [noparse][[/noparse] 黃鶴 ] in Taiwan
if you apply 12V square wave(50-500 kHz) with 50% duty cycle it will also draw x amps.
▔▔▔▔▔▔▔▔▔▔▔▔▔▔▔▔▔▔▔▔▔▔▔▔
Lots of propeller based products in stock at affordable prices.
··50 to 500khz. This is well above audible levels and is the kind of information I'm looking for. What does it take to smooth it out? I have never built a power supply and I read a post where Mike Green sited differences between electrolytic, tantalum and ceramic caps. Do I need a coil?
▔▔▔▔▔▔▔▔▔▔▔▔▔▔▔▔▔▔▔▔▔▔▔▔
The first thing you need to think about with power supply is how much power do you really need? Maybe double that and go window shopping.
Amps X volts = watts 3amps x 12 volts = 36watts, 6 amps x 60 volts = 360 watts, and so on
12volts at .4 amps really needs only 3 watts, but more is handy. 3amps at 12 volts is easily bought in a wall wart these days and about all I need. With those lead acid batteries, you can get a lot more though. I've got a couple of gel cells that are rated at 9amphours and for short spurts you can get much higher - but you have to have a large load (or a direct short - use fuses) on them to do so. So what exactly is your load going to be?
I used the TIP120 not because I actually need 5amps at 60 volts, but because I have the extra capacity if I ever need to drive a bigger motor, bigger stepper, or bigger relay.
In other words, I don't have build yet another project just because something is a little bit larger.
The same goes for power supplies, extra capacity is nice to have for later.
▔▔▔▔▔▔▔▔▔▔▔▔▔▔▔▔▔▔▔▔▔▔▔▔
Ain't gadetry a wonderful thing?
aka G. Herzog [noparse][[/noparse] 黃鶴 ] in Taiwan
··I only used 470 ohm pull-down resistor (b to e). I did not use a base resistor. I'll make that change.
▔▔▔▔▔▔▔▔▔▔▔▔▔▔▔▔▔▔▔▔▔▔▔▔
▔▔▔▔▔▔▔▔▔▔▔▔▔▔▔▔▔▔▔▔▔▔▔▔
Lots of propeller based products in stock at affordable prices.
A combination of experience and looking at a lot of examples. The TIP120 with a 4.7k pull-down and a 470 ohm base was from an Arduino schematic for a relay driver, but it works with one direction motors as a single use or for stepper motors when the required number are in parallel.
Previously, I had seen TIP110's in examples, but they are limited to less power control. For about the same money, it is easy to 'upsize' to control more power or have more headroom against failure.
So it seemed wisest to build as big as I could get away with with a minimal part count. Maybe even a larger TIP1xx could be used, but I just wanted to be sure I could drive 30amp rated 12 volt automotive relays amd the UNL2803 was likely not to do so.
I suspect some guys just stay stuck with using the UNL2803 and never look at a larger stepper motor. You've broken through that barrier and can take advange of using motors with more muscle.
Darlingtons do create more heat - that's why the shift to individual ones (I am using them without heat sinks for compactness).· On the other hand, power MOSfets can do the same - but in some cases are harder to drive and in other cases are easily damaged my mishandling. So I went for a simple rugged design that can easily drive 1 amp at a steady on for each channel.· Heat sinks start making the whole project rahter large.
▔▔▔▔▔▔▔▔▔▔▔▔▔▔▔▔▔▔▔▔▔▔▔▔
Ain't gadetry a wonderful thing?
aka G. Herzog [noparse][[/noparse] 黃鶴 ] in Taiwan
Post Edited (Loopy Byteloose) : 7/23/2010 12:18:47 PM GMT
With that said, a 12V stepper should only pull rated current if you drive it with 12V. I wonder what's wrong???
Anyways, if you PM me your email, I'll send you all I have on this. I'm using a readily available driver IC, IRF510 and related components. I have datasheets, schematics.... the whole nine-yards... I've already done a ton of research on this (which does NOT make me an expert)
PWM is pretty neat in that you use a small "sensing" resistor into a comparator. You monitor the voltage across the resistor at a frequency of about 20kHz to ??? and make changes as needed..... Pretty neat stuff. Most of the work is done inside an IC so that makes it MUCH easier. [noparse]:)[/noparse]
▔▔▔▔▔▔▔▔▔▔▔▔▔▔▔▔▔▔▔▔▔▔▔▔
"puff"...... Smile, there went another one.
Given that, speed on stepper motors is tricky as they have spots where they run smooth and spots where they run choppy. Fast has not been so much an issue as precise position with steppers - that is where they really are useful. But given PWM of the overall supply 24VDC at 50% duty cycle with provide the same amps as 12VDC at 100% on.
So is that really a 12V stepper or an X amp stepper or a Y watts stepper? "CNC Robotics" is a very useful reference.
▔▔▔▔▔▔▔▔▔▔▔▔▔▔▔▔▔▔▔▔▔▔▔▔
Ain't gadetry a wonderful thing?
aka G. Herzog [noparse][[/noparse] 黃鶴 ] in Taiwan
You want to PWM the overall supply to the UNL2803 that is driving a 400ma per coil (or 100ma per coil?) stepper motor because this smooths the rotation over the entire range of the whatever speed you run the steps at.
Yes, the TIP120 will work and work well for that.
Regarding the maximum voltage for a stepper motor, it is hard to say. But the maximum current is rated by the physical wire size and the ability of the motor's configuration to cool the coils. Not much is considered in the way of cooling because the motor is likely to be run very slow at times in a single step or holding mode. But still the overall heat build up is watts and equivalent to amps times volts. So a 12v stepper coil at 400ma is a 3 watt maximum is still a 3 watt maximum if you us 24volts or 48volts. The duty cycle is where you do your current limiting to prevent heat damage.
And so, keep the duty cycle according to the voltage you provide, but you can adjust the rate of PWM according to what gives the best performance.
I hope that this puts to rest most of your questions. Fortunately a 480ohm pull down with the TIP120 doesn't do any damage, but resistors are usually 1/4watt and 470ohms in the wrong place is likely to burn up in a flash. So review values before you insert them regardless of who provides the schematic. Also, 470 ohms is exceedingly strong for a pull up or pull down resistor. Think about purpose and context as well.
It just so happens the TIP120 with these values was in a PWM section of an Arduino tutorial. It should work fine.
If you are wondering about how to supply higher DC voltages, just use a transformer, a bridge rectifier, and a few ripple capacitors - the stepper motor doesn't have to have the kind of voltage regulation that digital circuitry required. But do use flyback diodes on each and every coil in addition to the protective diodes included in all the Darlingtons.
▔▔▔▔▔▔▔▔▔▔▔▔▔▔▔▔▔▔▔▔▔▔▔▔
Ain't gadetry a wonderful thing?
aka G. Herzog [noparse][[/noparse] 黃鶴 ] in Taiwan