Position Controller Kit question about encoder speed.
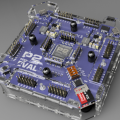
I intend to mount the Position Controllers onto my wheel chair motors. It is very convenient to mount them inside the bell housing on the end of the motor once the electromagnet clutch assembly is removed.
I looked through the documentation but could not find the max rpm that the encoder can handle. My motor will be spinning at up to around 2,500 rpm, which would be 1,500 counts per second.
Will it handle that rpm? If not, what is the max rpm?
Another concern is the Ramp speed. As I understand it the max ramp rate is 255 positions per second2. If that is correct then then it will take three seconds to reach the max rpm, and three seconds to come to a stop. I suppose the CLRP command can be used to make quicker stops. Either that or I can make a smaller encoder disk to decrease the resolution and counts per second.
Rich H
BTW, for my application each encoder count is .31 degrees of wheel rotation or .037" inches of travel. That makes for some pretty good resolution eh?
▔▔▔▔▔▔▔▔▔▔▔▔▔▔▔▔▔▔▔▔▔▔▔▔
The Simple Servo Tester, a kit from Gadget Gangster.
Post Edited (W9GFO) : 5/26/2010 8:32:31 PM GMT
I looked through the documentation but could not find the max rpm that the encoder can handle. My motor will be spinning at up to around 2,500 rpm, which would be 1,500 counts per second.
Will it handle that rpm? If not, what is the max rpm?
Another concern is the Ramp speed. As I understand it the max ramp rate is 255 positions per second2. If that is correct then then it will take three seconds to reach the max rpm, and three seconds to come to a stop. I suppose the CLRP command can be used to make quicker stops. Either that or I can make a smaller encoder disk to decrease the resolution and counts per second.
Rich H
BTW, for my application each encoder count is .31 degrees of wheel rotation or .037" inches of travel. That makes for some pretty good resolution eh?
▔▔▔▔▔▔▔▔▔▔▔▔▔▔▔▔▔▔▔▔▔▔▔▔
The Simple Servo Tester, a kit from Gadget Gangster.
Post Edited (W9GFO) : 5/26/2010 8:32:31 PM GMT
Comments
The Position Controllers should easily handle speeds around 2500 RPM (1500 pos/sec). During testing, the modules measured speeds in excess of 8000 RPM (4800 positions/sec).
For the ramp rate (acceleration/deceleration), the maximum value is (255 positions/0.5sec)/0.5sec which would be 255 positions/0.25sec^2, or 1020 positions/sec^2. So based on the equation:
a=(Vf-Vi)/t
converted into:
t=(Vf-Vi)/a
where Vi=0 (starting from a stop) and a=1020 pos/sec^2, then I get:
t=(1500 pos/sec)/(1020 pos/sec^2)
t=1.47 seconds
So to ramp up to full speed should take about 1.5 seconds. Would that be acceptable for your application? If you still need more control over your application, or if you are controlling your motors in more of a "speed control" fashion (rather than position control), then you may want to control your motor drivers directly in software and use the Position Controllers as a speed and position sensor (rather than controller).
Hope this answers your questions.
Sincerely,
-Kevin McCullough
Also good news that I miscalculated the ramping, I was using 255 steps/sec rather than 255 steps/0.5 sec.
Rich H
▔▔▔▔▔▔▔▔▔▔▔▔▔▔▔▔▔▔▔▔▔▔▔▔
The Simple Servo Tester, a kit from Gadget Gangster.