Propeller PCB Layouts - Sample layouts for DIP40 & QFP44
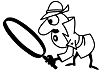
There has been a lot of questions regarding correct pcb layout and decoupling. No one design is necessarily better than another. However, there are lot of designs that leave much to be desired. PCB layout is something that is learned over many years of testing.
Here are my solutions...
The TriBlade design uses 100nF X7R ceramic mono at each end of the DIP40. In reality, I then pour the ground plane, but the basic design shows where the power and ground traces are. Under the propeller I place·a 10nF X7R ceramic mono and 10uF tantalum. Note that the 10nF & 10uF help but the circuit runs quite well without them provided you do not overclock. This is most likely due to the remainder of the circuit.
The RamBlade design uses C2,3,4,5 100nF X7R ceramic mono for each of the power/ground pairs of the propeller QFP. An additional C1·10nF X7R ceramic mono and C9 10uF tantalum round out the decoupling. Note the power comes into the prop on a single line on the topside beside C2 and does not go to any other chip from here. Under the prop (botomside - same as the prop chip) is a ground plane. Under the prop (topside - opposite side to the prop chip) is a power plane. A ground plane surrounds the prop on both sides. The crystal leads are thicker and short and are surrounded by ground plane on both sides of the pcb. The vias between the xtal and prop chip connect the gorund planes on both sides.
Use of these layouts is (c) and use for non-commercial designs is permitted.
I hope this helps
▔▔▔▔▔▔▔▔▔▔▔▔▔▔▔▔▔▔▔▔▔▔▔▔
Links to other interesting threads:
· Home of the MultiBladeProps: TriBlade,·RamBlade,·SixBlade, website
· Single Board Computer:·3 Propeller ICs·and a·TriBladeProp board (ZiCog Z80 Emulator)
· Prop Tools under Development or Completed (Index)
· Emulators: CPUs Z80 etc; Micros Altair etc;· Terminals·VT100 etc; (Index) ZiCog (Z80) , MoCog (6809)·
· Prop OS: SphinxOS·, PropDos , PropCmd··· Search the Propeller forums·(uses advanced Google search)
My cruising website is: ·www.bluemagic.biz·· MultiBlade Props: www.cluso.bluemagic.biz
Here are my solutions...
The TriBlade design uses 100nF X7R ceramic mono at each end of the DIP40. In reality, I then pour the ground plane, but the basic design shows where the power and ground traces are. Under the propeller I place·a 10nF X7R ceramic mono and 10uF tantalum. Note that the 10nF & 10uF help but the circuit runs quite well without them provided you do not overclock. This is most likely due to the remainder of the circuit.
The RamBlade design uses C2,3,4,5 100nF X7R ceramic mono for each of the power/ground pairs of the propeller QFP. An additional C1·10nF X7R ceramic mono and C9 10uF tantalum round out the decoupling. Note the power comes into the prop on a single line on the topside beside C2 and does not go to any other chip from here. Under the prop (botomside - same as the prop chip) is a ground plane. Under the prop (topside - opposite side to the prop chip) is a power plane. A ground plane surrounds the prop on both sides. The crystal leads are thicker and short and are surrounded by ground plane on both sides of the pcb. The vias between the xtal and prop chip connect the gorund planes on both sides.
Use of these layouts is (c) and use for non-commercial designs is permitted.
I hope this helps

▔▔▔▔▔▔▔▔▔▔▔▔▔▔▔▔▔▔▔▔▔▔▔▔
Links to other interesting threads:
· Home of the MultiBladeProps: TriBlade,·RamBlade,·SixBlade, website
· Single Board Computer:·3 Propeller ICs·and a·TriBladeProp board (ZiCog Z80 Emulator)
· Prop Tools under Development or Completed (Index)
· Emulators: CPUs Z80 etc; Micros Altair etc;· Terminals·VT100 etc; (Index) ZiCog (Z80) , MoCog (6809)·
· Prop OS: SphinxOS·, PropDos , PropCmd··· Search the Propeller forums·(uses advanced Google search)
My cruising website is: ·www.bluemagic.biz·· MultiBlade Props: www.cluso.bluemagic.biz
Comments
▔▔▔▔▔▔▔▔▔▔▔▔▔▔▔▔▔▔▔▔▔▔▔▔
*Peter*
BTW the TriBlade with the 100nF at each end of the chip (and good decoupling throughout the pcb) actually operates at 6.5MHz without the extra 10nF & tantalum under the DIP. It also runs at 13.5MHz * 8 (108MHz) although I would say not proven.
As I understand, your designs use a seperate regulator for the propeller and this would account for some relaxation of the capacitor requirements.
I have noticed on recent low powered chips that the manufacturers are increasingly recommending a 100nF and a tantalum at the supply pins because of increased switching transients due to the power up/down of internal circuits to save power. This is what the propeller chip has been doing for a few years now
▔▔▔▔▔▔▔▔▔▔▔▔▔▔▔▔▔▔▔▔▔▔▔▔
Links to other interesting threads:
· Home of the MultiBladeProps: TriBlade,·RamBlade,·SixBlade, website
· Single Board Computer:·3 Propeller ICs·and a·TriBladeProp board (ZiCog Z80 Emulator)
· Prop Tools under Development or Completed (Index)
· Emulators: CPUs Z80 etc; Micros Altair etc;· Terminals·VT100 etc; (Index) ZiCog (Z80) , MoCog (6809)·
· Prop OS: SphinxOS·, PropDos , PropCmd··· Search the Propeller forums·(uses advanced Google search)
My cruising website is: ·www.bluemagic.biz·· MultiBlade Props: www.cluso.bluemagic.biz
Post Edited (Cluso99) : 4/9/2010 4:16:13 AM GMT
1. Can I/O lines and power line go underneath a crystal?
2. If you're making a 2 sided PCB with components only on one side, where would you put the fourth decoupling capacitor that is supposed to go across the VDD/VSS leads right next to XO/XI?
3. Is it safe to run power and I/O lines underneath the Propeller?
4. Is decoupling capacitors for each VDD/VSS pair necessary, or just one or two?
5. Besides short crystal traces and decoupling capacitors, are there any other considerations needed for overclocking?
6. Besides the mechanical mounting options, is there any difference between SMD and through hole crystals?
2. Difficult answer. If you have a ground and power plane under the prop and that joins all 4 VDD and all 4 VSS (as it should) then you can often get away with 1 or 2 caps. I prefer to keep my power away from xtal traces.
3. I don't like placing IO lines under the prop because I have gnd on one side and power on the other. Sometimes it is unavoidable.
4. You can get away with 2 (100nF and 10uF). Parallax did use 1x 1uF previously. Not sure about nowadays. Depends on the frequency.
5. Any other pins running at high speed need to be carefully traced and short.
6. Not really. T/h are slightly smaller because they dont have the smt pads (for typical HC49U/S) and are easy to get. I socket my xtals.
Remember, I am pushing the prop to its limits, so I am using an overkill design to ensure I don't have problems. My main overclocked pcbs have SRAM and that is clocked at these speeds.
Critical nets like supply and ground connections should be routed first. Get them right, and you are unlikely to have problems. My home-made prototype boards (I've made three or four using the Propeller in DIL and QFP) are usually single-sided, without copper pour, and they work OK. I don't overclock them, though. I might try it.