Math/geometry question about positional accuracy wrt delta robots
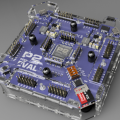
I'm thinking about building a delta robot similar in size to this commercially available one in the video.
DesktopDelta video
A simulation
I would use high performance digital servos with zero dead band.
The arms would connect directly to the servo output shaft and would move through about 90 degrees of arc. That would correspond to 900 unique positions for one arm.
If the intended workspace is 9" in diameter that would roughly equate to .010" resolution if it were a linear relationship. Of course it is not linear and there are a total of three servos contributing.
My question is, which I can't wrap my mind around, how does the combination of the three servos affect the ultimate accuracy?
Would the accuracy be better than .010" considering the other two servo's input?
Towards the edges of the workspace, does the accuracy diminish? When the head is directly under a servo, that servo contributes little to the X/Y positioning but a great deal to the Z, the other two then contribute more to the X/Y and the geometry of their arms is in a position to offer the greatest resolution.
I need to figure out the relationship between positional accuracy (given .1 degree resolution of the arms) and the size of the work area. I am after .010" or better accuracy.
Rich H
Post Edited (W9GFO) : 8/16/2009 6:11:15 PM GMT
DesktopDelta video
A simulation
I would use high performance digital servos with zero dead band.
The arms would connect directly to the servo output shaft and would move through about 90 degrees of arc. That would correspond to 900 unique positions for one arm.
If the intended workspace is 9" in diameter that would roughly equate to .010" resolution if it were a linear relationship. Of course it is not linear and there are a total of three servos contributing.
My question is, which I can't wrap my mind around, how does the combination of the three servos affect the ultimate accuracy?
Would the accuracy be better than .010" considering the other two servo's input?
Towards the edges of the workspace, does the accuracy diminish? When the head is directly under a servo, that servo contributes little to the X/Y positioning but a great deal to the Z, the other two then contribute more to the X/Y and the geometry of their arms is in a position to offer the greatest resolution.
I need to figure out the relationship between positional accuracy (given .1 degree resolution of the arms) and the size of the work area. I am after .010" or better accuracy.
Rich H
Post Edited (W9GFO) : 8/16/2009 6:11:15 PM GMT
Comments
To be more general, you could formulate·an expression for each of the components x, y, z·as functions (probably trigonometrical functions)·of the three (or however many) servo angles θ1, θ2 ,θ3, with an error term Δ1, Δ2, Δ3 added for each of the servo angles.· Derive an expression for the total position error as a function of θ1, θ2, θ3, Δ1, Δ2, Δ3.· Calculate the maximum for this function (the maximum will occur where the first derivative equals zero), and that's your maximum position error.
Simple, no?
▔▔▔▔▔▔▔▔▔▔▔▔▔▔▔▔▔▔▔▔▔▔▔▔
· -- Carl, nn5i@arrl.net
Post Edited (Carl Hayes) : 8/17/2009 2:01:39 PM GMT
If the servo's perpendicular location is 5" above the surface, a simple tangent calculation shows that between 0 and 0.1 degrees (servo arm pointing perpendicular to the surface) you have 0.00035" resolution, and between 44.9 and 45 degrees you have 0.0007" resolution. So you half the resolution when the servo is at 45 degrees, compared to straight down.
▔▔▔▔▔▔▔▔▔▔▔▔▔▔▔▔▔▔▔▔▔▔▔▔
Don't worry. Be happy
You mention that the servo resolution is 0.01 degree, so you can set·Δ1=Δ2=Δ3=0.572957795131 (the angle 0.01 degree expressed in radians).· Thus the· Δ1, Δ2, Δ3 are constants, not variables.· Indeed, you might be able to use half this value if the linearity and the differential linearity of the servos are perfect.
▔▔▔▔▔▔▔▔▔▔▔▔▔▔▔▔▔▔▔▔▔▔▔▔
· -- Carl, nn5i@arrl.net
▔▔▔▔▔▔▔▔▔▔▔▔▔▔▔▔▔▔▔▔▔▔▔▔
Don't worry. Be happy
No, that does not look simple!
In high school I excelled in geometry but barely passed algebra and I never took trig. I've learned more about algebra from my kids than I ever did in school.
Heck I feel smarter for just having an idea what you were talking about!
Looks like I'm going to have to do some studying - and draw lots of pictures.
@dev/null, the example you gave where the arm is perpendicular to the surface is where there is the greatest accuracy, in that position the head would be furthest from the center. When all three arms are at 45 degrees the head would be centered.
At any rate I have a better idea on how to figure this out. Thanks guys!
Rich H
I should've said repeatability in the beginning, if I can get it to go to the same spot time after time and not miss by more than .005" then all will be good.
Rich H
▔▔▔▔▔▔▔▔▔▔▔▔▔▔▔▔▔▔▔▔▔▔▔▔
Don't worry. Be happy