3.3V and 5V sensor voltage requirements: Parallax customer input requested!
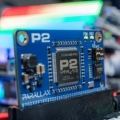
Hey there,
We're designing a small breakout board with the VTI SCP1000 Pressure Sensor (0-30K feet above msl). This sensor requires a 3.3V power supply.
Propeller users will have 3.3V·and 5V power supplies·on all of·our demo boards. BASIC Stamp·boards have only 5V power supplies. As time passes and we will produce more breakout boards·based upon·prior designs. My personal preference is to keep the designs simple and raw (no voltage regulator), clutter-free and with the minimum passive component/adapter board·circuitry needed to use the device.
To some·customers this isn't usable out of the bag because they need 3.3V.
Would BASIC Stamp programmers be happy if we had a·breadboard-friendly 3.3V regulator in our component shop and didn't include this in·the design?
Propeller customers okay without a regulator?
Your input is welcome and appreciated.
Thank you,
Ken Gracey
·
We're designing a small breakout board with the VTI SCP1000 Pressure Sensor (0-30K feet above msl). This sensor requires a 3.3V power supply.
Propeller users will have 3.3V·and 5V power supplies·on all of·our demo boards. BASIC Stamp·boards have only 5V power supplies. As time passes and we will produce more breakout boards·based upon·prior designs. My personal preference is to keep the designs simple and raw (no voltage regulator), clutter-free and with the minimum passive component/adapter board·circuitry needed to use the device.
To some·customers this isn't usable out of the bag because they need 3.3V.
Would BASIC Stamp programmers be happy if we had a·breadboard-friendly 3.3V regulator in our component shop and didn't include this in·the design?
Propeller customers okay without a regulator?
Your input is welcome and appreciated.
Thank you,
Ken Gracey
·
Comments
Oh, another thing. I suppose it should go into the new products page, but one thing that I'd like to see parallax carry are the small jumpers to jump headers. I know Mouser and other places carry them, but I'd prefer to order from Parallax...
John Abshier
Here's how I handle that with my daughterboards: Each daughterboard has a 5V and a Vdd input. Sometimes Vdd is 3.3V; sometimes, 5V, and the board has to work both ways. There are three situations that have to be addressed:
1. Board contains components that will run on 3.3V or 5V interchangeably: use the Vdd input with no add'l regulation.
2. Board contains 5V-only components: power the board from the 5V input and interface with 3.3V-compatible (e.g. 74HCT) interface logic, if necessary.
3. Board contains 3.3V-only components: power the board from 5V and include an onboard 3.3V regulator. Use 5V-tolerant (e.g. 74LVC) interface logic, if necessary.
I definitely think you need to provide a canned regulator solution. I've seen way too many threads in these forums dealing with misapplied linear regulators, often due to poorly-chosen caps. Having a drop-in solution, with the proper caps, would eliminate a lot of tech support calls (and the expense associated with each one).
There are some regulators that use MOSFET pass transistors and have almost zero dropout voltage at modest currents. You could easily feed these with either 5V in or 3.3V in and still get 3.3V out — no jumpers required. That would simplify the user interface enormously.
-Phil
Since I've started down the path of OTness, I thought I'd add one more thing: The Propeller page http://www.parallax.com/tabid/407/Default.aspx lists the 1.0 version of the datasheet for download, but the current version is 1.2.
Post Edited (SRLM) : 6/8/2009 9:00:42 PM GMT
All new products can be found on this page http://www.parallax.com/tabid/753/Default.aspx. You can navigate to this page from the front page of the Parallax site (beneath the three square images). You have the option of visiting a page displaying new products, featured products, or subscribing to the RSS feed.
Thank you very much for telling us about the datasheet. We have updated the web.
Kind Regards,
Lauren
▔▔▔▔▔▔▔▔▔▔▔▔▔▔▔▔▔▔▔▔▔▔▔▔
·
Lauren Davis
Marketing Manager
Parallax, Inc.
916-624-8333
ldavis@parallax.com
·
In addition to the cost factor for one sensor, as more 3.3 products become available, why should we have multiple 3.3 volt regulators on each sensor?
I'm sure the Parallax documentation team can make putting a 3.3 volt regulator on something like the BOE so simple that even a toddler can do it. (The human kind, not the mechanical version)
▔▔▔▔▔▔▔▔▔▔▔▔▔▔▔▔▔▔▔▔▔▔▔▔
John R.
Click here to see my Nomad Build Log
humanoido
The second issue faced when making a product compatible with both 5V and 3.3V systems in minor differences in operation cause by running the device at 3.3V when it has a 3.3V LDO regulator for 5V operation. Some devices are affected either in operation, calibration or both by the supply voltage. When operating from a 5V supply the 3.3V regulator drops the voltage down to 3.3V and everything is fine. But when you apply 3.3V there is a small voltage drop and the device is now running at anywhere from 3.0V – 3.27V depending on the LDO used. This can affect devices that use the supply voltage as a reference, such as modules containing an ADC. This then introduces potential calibration issues. Realistically some of these devices may work on the BASIC Stamp but really may benefit from a faster microcontroller such as the Propeller anyway. These are just some things to keep in mind on this topic. It is also why many experimenter and break-out boards don’t have this circuitry included and are very minimal.
▔▔▔▔▔▔▔▔▔▔▔▔▔▔▔▔▔▔▔▔▔▔▔▔
Chris Savage
Parallax Engineering
Take a look at the MIC5203. It's an inexpensive LDO with a PNP pass transistor, and it's stable with cheap ceramic caps. At the SCP1000's current requirement, for example, the dropout voltage is almost nil. Also, most 3.3V devices will run at 3.0V, so if consistent analog calibration is necessary, you will get better regulation at 3.0V with a 3.3V supply.
I've seen so many instances in the forum where regulators are misapplied, often due to inappropriate capacitors. Given the choice, I'd make a sensor module as drop-in easy to apply as possible.
-Phil
What you suggest here seems good to me - especially with Parallax's (always excellent) documentation.
On the product info page, a simple link to the 3.3v regulator for Stamp Users and those with 5v systems along with the diagram for proper hook-up would be great. I think that Parallax selling the regulator would be nice for folks who might not know how to go about·looking for this and the documentation could show them how to do it (and maybe some sample or test code).
The whole thing would also be educational and make novice users aware of the issues involved.
▔▔▔▔▔▔▔▔▔▔▔▔▔▔▔▔▔▔▔▔▔▔▔▔
Whit+
"We keep moving forward, opening new doors, and doing new things, because we're curious and curiosity keeps leading us down new paths." - Walt Disney