Using Solder Baths
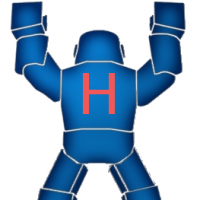
Hi guys,
1. How many of you actually use solder baths?
2. Can solder baths be used to quickly solder small boards?
3. My solder surface kept on getting a layer of dirt a few seconds after the solder paste has dried. How do I prevent this?
4. Each time I add solder paste to the bath to make the solder not so dry, the whole room fills with flux smoke.
How do I keep the solder wet without the smokes?
Thanks.
▔▔▔▔▔▔▔▔▔▔▔▔▔▔▔▔▔▔▔▔▔▔▔▔
www.fd.com.my
www.mercedes.com.my
1. How many of you actually use solder baths?
2. Can solder baths be used to quickly solder small boards?
3. My solder surface kept on getting a layer of dirt a few seconds after the solder paste has dried. How do I prevent this?
4. Each time I add solder paste to the bath to make the solder not so dry, the whole room fills with flux smoke.
How do I keep the solder wet without the smokes?
Thanks.
▔▔▔▔▔▔▔▔▔▔▔▔▔▔▔▔▔▔▔▔▔▔▔▔
www.fd.com.my
www.mercedes.com.my
Comments
You should use solid solder, not solder paste, in a solder bath.
Leon
▔▔▔▔▔▔▔▔▔▔▔▔▔▔▔▔▔▔▔▔▔▔▔▔
Amateur radio callsign: G1HSM
Suzuki SV1000S motorcycle
0. Using Kapton tape, mask any plated areas on the bottom of the board that you don't want exposed to the solder (e.g. mounting holes, gold fingers, etc.).
1. Insert all the parts.
2. Spray the underside of the board with flux. I used a little plastic spray bottle that could be pumped up by hand to pressurize it.
3. Suspend the wet board over an electric pancake griddle to preheat the board and dry the flux.
4. Just before dipping the board, take a piece of cardboard and use it like a squeegee to draw the solder dross (what you call "dirt") to one end of the bath and up over the edge. (You have to keep the bath full to do this.)
5. With aluminum tongs, dip the board into the solder. The board will tend to float, so you'd have to work to push it in too far. Count to three and pull it out.
6. Once the solder has set, trim all the leads, remove the Kapton tape, and you're done. (I visited a company once that had a little homemade machine they put the boards into that trimmed the leads with a rotating blade, like a lawnmower.)
That's all there is to it. It's fast, much cheaper than a wave solder machine, and produces "factory perfect" solder joints. But if you use this method, HAVE A GOOD EXTRACTION FAN RUNNNG AT ALL TIMES. The lead fumes are bad enough, but the chemicals in the fine flux mist could send an elephant into spasms. It's really nasty stuff!
-Phil
Post Edited (Phil Pilgrim (PhiPi)) : 5/10/2009 7:38:57 PM GMT
Is the pre-heating of the board really necessary?
Is Kapton tape the same as electrical tape?
Can we solder double sided boards with a solder bath?
I heard some people use "smokeless flux". Does it exist?
Thanks.
▔▔▔▔▔▔▔▔▔▔▔▔▔▔▔▔▔▔▔▔▔▔▔▔
www.fd.com.my
www.mercedes.com.my
Yes, the preheating is necessary.
No, electrical tape is made of vinyl, which would melt and make a gooey or crusty mess on the board. Kapton is a clear yellowish-colored polymer that will survive the high temp of the solder bath.
By double-sided, do you mean "components on both sides"? If so, the answer is no. But if you just mean "traces on both sides", sure. The board does have to be solder-masked, though.
I don't know anything about smokeless flux.
-Phil
I worked in this industry for 5 years - I never heard of smokeless flux. Sounds like something dreamed up by the marketing department [noparse];)[/noparse]