RC sub/ underwater ROV thing
Ok iv come here for help before and have always gotten plenty, but I still could never get whatever it was I was working on to work that was all with a BS1.
For about the past month we have been using the BOE-Bot platforms in DE class and I have to say threes just something about the way that book is laid out that makes everything click and make since. I also think it has to do with the fact that it’s a BS2 I don’t know what but it’s just been easier. ··
So anyway to my point Thursday was our last day and we got to keep our Boe-Bots so I was so excited and i also got two more from these kids that said they would never use threes. ··
I have all this stuff to build an RC sub/ROV whatever you want to call it. And I’m sure I’ll have some more questions but my main one is how do I send a signal to the sub. I was thinking RF transceivers but I don’t know how good they would work under water.· Anyone know? And I also had the idea of sending dada back and forth with sound through the use of waterproof ultrasonic sensors. http://futurlec.com/Ultrasonic_Sensors.shtml·I talked to a guy about it he said it could work but he never got back to me as to how I’d do it. The ultrasonic sensors would be a lot cheaper and I think if I could get it to work the signals would travel a lot better and farther under water.
My “plan” is to have one BS2 above water hooked up to all the controls that I will make with various switches and sliders. And the other one will be in the sub obviously. So somehow say I have a liner pot for speed control ill have to convert that to a PWM number and send it to the sub, or if I want to turn on the lights ill have to send that command. The thing I’m wondering is if you do have a transceiver setup can it send more than one command at a time. I bet it sends them one at a time but it’s so fast you might as well say it’s at the same time right? ·
Well I know that was a long one but I’m hoping you now have a good understanding of what I want to accomplish. Any questions for me I’d love to answer them.
I hope someone will stay tuned because though it may not be right away i know I’ll need help with something or another.
·
I’d love to draw up a block diagram of my whole idea and show it to you all but it’s pretty late and I need to get going so here are some random pics of a few things iv been looking into. It just looks like a pipe now but I have big plans for this thing.
By the way in case you’re wondering its 4” I.D x 50” Long
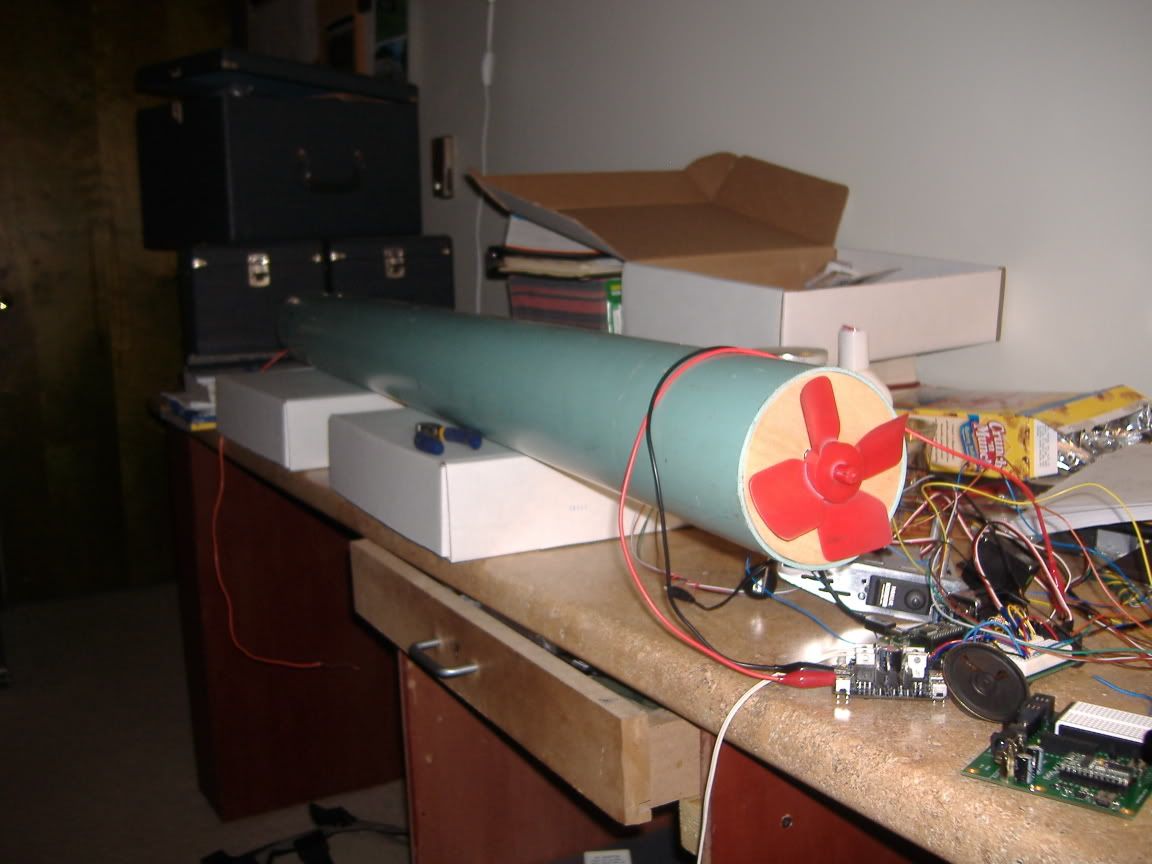
Mounted the prop just for speed controller testing works great. Also note old school game controller picked it up for 25 cents
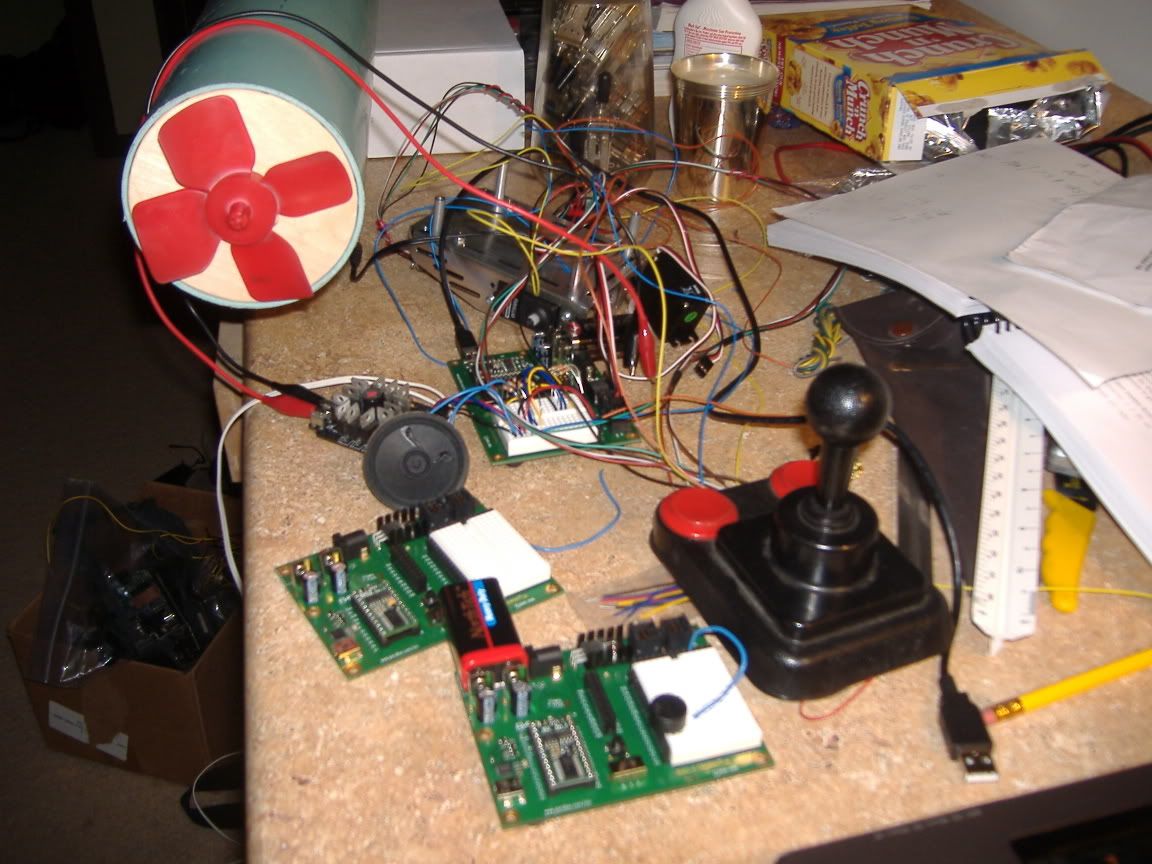
This is the camera i plan to take apart more and place in front, i like it because its super clear and i hope to hook up the zoom buttons.
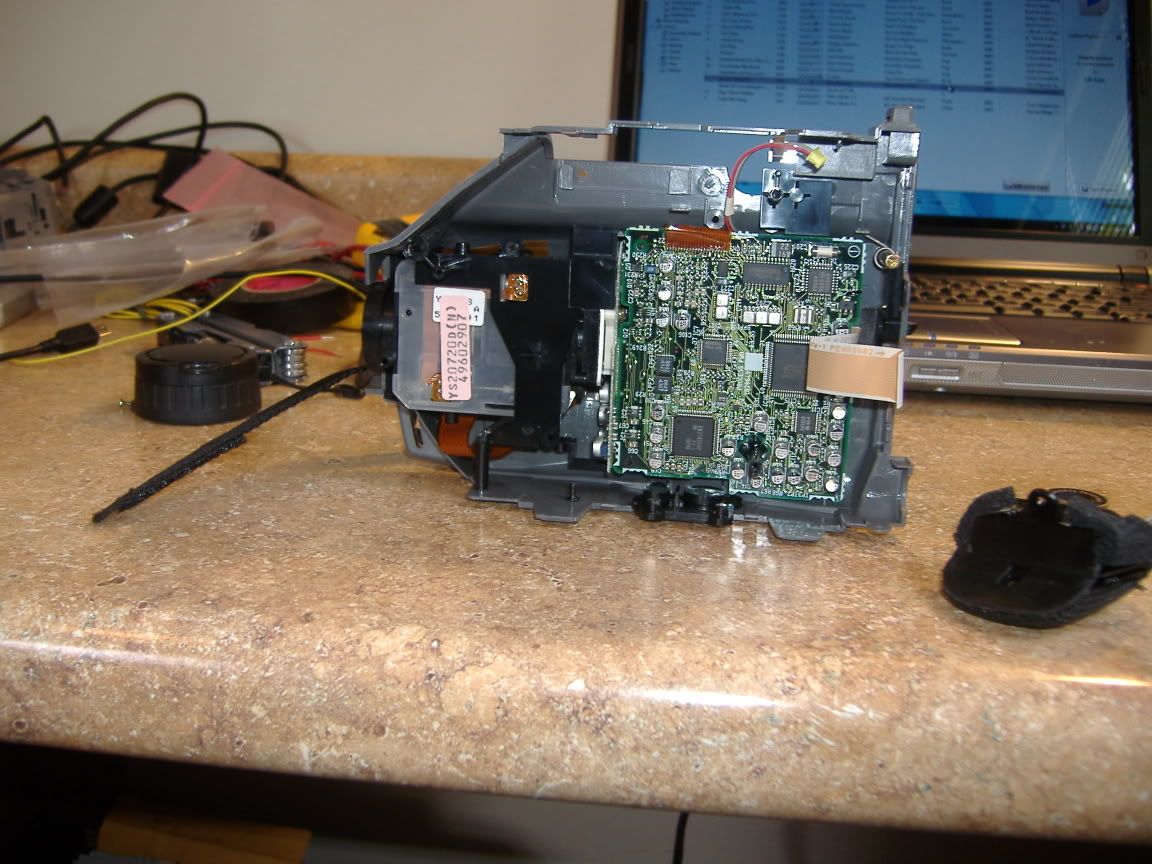
▔▔▔▔▔▔▔▔▔▔▔▔▔▔▔▔▔▔▔▔▔▔▔▔
There are no Undo buttons in life.
Comments
▔▔▔▔▔▔▔▔▔▔▔▔▔▔▔▔▔▔▔▔▔▔▔▔
- Stephen
Radio transmitters are commonly used in fisheries research. See Lotek's products for some of applications of sending sending coded data. One of the problems with radio transmitters is that salt water attenuates the signal really quickly - so that route would be limited to fresh water. Unless you're planning to deploy in a bay or something, you should be ok.
One option to get around the submerged transmission problem is to have the vehicle run a leg and then surface. You can communicate wirelessly on the surface - perhaps providing new waypoints, and then let it run another leg. Perhaps during the surface interval, the vehicle could transmit and sensor data back.
Acoustic modems have been researched by places like WHOI (look at their acoustics group) and have become pretty well established from what I can understand of the field. Acoustics (ultrasonics) will work well in both fresh and salt water, but you need to think about echoes from the sound bouncing off the bottom or water surface and things like that a bit. However, companies like Vemco and Lotek can transmit the ID's of tags on fish via sound pretty successfully, so I hazard a guess that you may have some luck with it.
When I asked a similar question in the Sandbox Forum, someone suggested just getting a couple of ultrasonic transducer sets talking to one another. That's the direction I hope to take to work out the approach. Once you've got that, the door is pretty much open.
Another entirely different thing to think about is the basic configuration of your ROV/AUV. While there are some really nice examples of the 'torpedo' format (REMUS, Slocum Gliders, etc), there are a few others that are very different (like ABE, the SeaRay lines, and even the vaguely "cube-ular" ROVs high schoolers build out of pvc piping). Some of these platforms are super maneuverable and some are great for long distances.
Anyway, there are many many submerged applications and a number of national competitions for AUVs and ROVs. It's a very interesting area and I'm looking forward to learning from what you're doing!
And I said ROV because it will be remotely operated, I really don’t know what to call it yet. And Franklin by open water you mean away from the sub a bit? I have already taken that into account but thanks that’s the type of input I’m looking for. Like I said I just mounted it to get a feel for what it might look like, test the speed controller and also I didn’t have a longer shaft till today. ·I went to Menards for about an hour and found some really cool parts. I will upload some pictures and add captions in a bit. ·
So I think ill order some ultrasonic sensors and just try it out under some water tough I have no idea how to transmit data from one board to another. ·Maybe someone has a link I could take a look at. Dose anyone know for sure if RF could-might-may-dose-will·work??? Also any ideas as to what I could add to this thing would be great like various sensors and such.
What the back will most likely look like along with fins that i have yet to make, im thinking PVC plate or something·i dont know yet, i mean what would be a good material to make them out of.
Drain cover thingy that I found should work well to protect the prop from weeds and stuff. It has threads so I’ll be able to thread it on/off easily. Also i have this metal circular grate thing that ill mount on the back to fully cover it.
·
Drain cover thingy that I found should work well to protect the prop from weeds and stuff. It has threads so I’ll be able to thread it on/off easily.
Propeller on .125” shaft going through .125” copper pipe filled with faucet and valve grease should make the motor to proper connection water tight. In theory have yet to test it.
I’m going to mount a piece of Plexiglas, or acrylic in this and position my camera behind that along with inferred and white LED's
12v DC motor from ink jet printer pretty fast and strong .125" shaft, Note table saw accident at work today throbs like no other.
Old speed controller i got from our robotics team, Victor 884 PWM controlled. There has to be a way to make your own????????
▔▔▔▔▔▔▔▔▔▔▔▔▔▔▔▔▔▔▔▔▔▔▔▔
There are no Undo buttons in life.
A table saw, at work?· I think that's an "OSHA reportable."
You should never push stock with your hand, use a push-stick.
Now that all thats cleared up we can get back on subject, anyone???
▔▔▔▔▔▔▔▔▔▔▔▔▔▔▔▔▔▔▔▔▔▔▔▔
There are no Undo buttons in life.
"Poly Steal"?· What's a "Concert home"?
In a shop, the operator is responsible for tool set-up
before he begins the operation.· Assume nothing.· You
don't need fancy tools like these, you could make your
own from scrap wood.· This way you'll have fingers to
push the "Undo buttons" once they become available.
▔▔▔▔▔▔▔▔▔▔▔▔▔▔▔▔▔▔▔▔▔▔▔▔
Time·─ Space·─ Gravity·─ Darkness·─ Death
Oh yeah here http://www.polysteel.com/
▔▔▔▔▔▔▔▔▔▔▔▔▔▔▔▔▔▔▔▔▔▔▔▔
There are no Undo buttons in life.
So here are my thoughts on this - maybe someone with more experience can correct or add:
Radio will work if you aren't in salty water.
If you've got salty water (like in a bay with a salinity of 20 or so), you can still get a signal but the range is MUCH reduced.
You'd basically need to be shallow (a few feet), and on top of the ROV.
Higher frequencies get damped out faster than lower frequencies.
So you need a fairly low frequency radio signal.
Since your using a low frequency signal - you're going to be limited in the amount of information you can send back and forth.
So try to program responses to simple signals (think yes/no or morse code or something similar).
Do a couple of google searches on Radio Telemetry and Underwater Radio Transmitters - you'll find enough to get you started.
If you've got a lake nearby and want to deploy there this summer, one of the more interesting sensors will be a temperature probe. I'm not going to tell you why!
Put the receiver in a something water tight and sink it - see if you can talk to it.
Do some range tests (if you can) to see how far away it'll work.
When you get this built be sure to have a 'fail safe' so that if you lose contact, your sub will come to the surface for retrieval
Well there fairly cheap so ill just order them and see.
▔▔▔▔▔▔▔▔▔▔▔▔▔▔▔▔▔▔▔▔▔▔▔▔
There are no Undo buttons in life.
It looks like the frequencies used are lower than the sparkfun t/r pair mentioned - around 100 mHz (saw some ranging from 95 to about 150).
Also, every underwater radio tag (transmitter) I've ever seen has an external antenna.
The length of the antenna is related to the wavelength of the signal.
▔▔▔▔▔▔▔▔▔▔▔▔▔▔▔▔▔▔▔▔▔▔▔▔
There are no Undo buttons in life.
The antenna can be coiled, and so can fit in very small spaces.
Study this: fish datalogger
You'll see underwater tags about the same size as those normally used on pets, including this picture-
▔▔▔▔▔▔▔▔▔▔▔▔▔▔▔▔▔▔▔▔▔▔▔▔
There are no Undo buttons in life.
▔▔▔▔▔▔▔▔▔▔▔▔▔▔▔▔▔▔▔▔▔▔▔▔
There are no Undo buttons in life.
Non-RFID radio tags can be seen at http://www.lotek.com/images/mcft-4.jpg
http://thinkorthwim.com/2006/10/22/sawstop-table-saw-brake/
▔▔▔▔▔▔▔▔▔▔▔▔▔▔▔▔▔▔▔▔▔▔▔▔
·"If you build it, they will come."
▔▔▔▔▔▔▔▔▔▔▔▔▔▔▔▔▔▔▔▔▔▔▔▔
There are no Undo buttons in life.
Now, fingers are worth way more than $100, so it's a valuable device, but only for people who aren't cheap and acknowledge that accidents can happen. Which his boss sounds like he's not that kind of person.
So anyway i got some parts for the ballast system today so I’ve got to figure that out. Any ballast ideas of your own I’d love to hear them. I’m going to use compressed air that will fill a balloon forcing water out of a chamber and by deflating it will pull water back into the chamber causing the sub to dive.
▔▔▔▔▔▔▔▔▔▔▔▔▔▔▔▔▔▔▔▔▔▔▔▔
There are no Undo buttons in life.
▔▔▔▔▔▔▔▔▔▔▔▔▔▔▔▔▔▔▔▔▔▔▔▔
There are no Undo buttons in life.
So I was talking to a friend and he told me about these waterproof motors and propellers he had. They were from a blow up pool toy that you sat on and it propelled you around. So he came over and we tested them in my tank.· All we did was hold onto them and apply power they were supper strong. So I decided to keep them and replace what I had before.
That leads me to my question does anyone have a good schematic for a PWM controlled 12v DC motor speed controller. ·I have one that was left over from this year’s robotic computation. But now that I’m going to use two motors I should have matching controllers. ·It couldn’t be that hard to build one. All I see on this professionally ·made one is 12 transistors or power mosfets a cap and a few other things.
I would just buy a couple but there so expensive and I get more out of building my own stuff.·
·
These are the new motors and propellers, you can see how much better they are from the original red one.
▔▔▔▔▔▔▔▔▔▔▔▔▔▔▔▔▔▔▔▔▔▔▔▔
There are no Undo buttons in life.
I am looking to make a land based robot switch to basic stamp program once it goes out of range of my 75MHz transmitter
I am sure there are simple answers but these things are quite large and powerfull
also I have to consider relaying signals couldn't a transmitter be wired to one receiver use a basic stamp progam to the hacked tx with variable pots
that will then transmit on a second frequicy to the bot itself
boat motor controller there I have found waterproof controlles for aroud $30
if you get a chance to use a trolling motor that would get some power tru the water
great looking work by the way