Flywheel Energy Storage
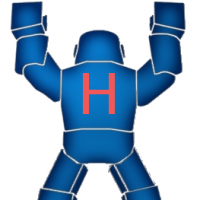
Beau or anybody,
I am thinking of constructing a flywheel supported by bearings and connected to the Parallax stepper motor.
I hope to use the stepper motor for dual purpose,
1. To use energy from Solar Panels (total 400 watts) to turn the flywheel during daytime
2. To become a generator during night to supply power for LED lightings.
Do you think such a concept is feasible?
How many RPMs can the stepper motor achieve?
What would be the best weight and diameter of the flywheel?
Thanks.
▔▔▔▔▔▔▔▔▔▔▔▔▔▔▔▔▔▔▔▔▔▔▔▔
www.fd.com.my
www.mercedes.com.my
I am thinking of constructing a flywheel supported by bearings and connected to the Parallax stepper motor.
I hope to use the stepper motor for dual purpose,
1. To use energy from Solar Panels (total 400 watts) to turn the flywheel during daytime
2. To become a generator during night to supply power for LED lightings.
Do you think such a concept is feasible?
How many RPMs can the stepper motor achieve?
What would be the best weight and diameter of the flywheel?
Thanks.
▔▔▔▔▔▔▔▔▔▔▔▔▔▔▔▔▔▔▔▔▔▔▔▔
www.fd.com.my
www.mercedes.com.my
Comments
(in Watts)
Anyway, the servo probably isn't such a good choice for motor.
I'm not certain it can be used as a generator, and it's built for keeping one speed.
And it's probably not the right size, either.
(It needs to be able to handle the 'max throughput' both as a motor and as a generator)
▔▔▔▔▔▔▔▔▔▔▔▔▔▔▔▔▔▔▔▔▔▔▔▔
Don't visit my new website...
Some basic physics.
When we are talking about energy stored in a rotating mass the energy (E) in joules is
E=1/2*I*w^2
where
I=mass moment of inertia=1/2 m r^2 for a solid disk
w=rotation speed in radians/sec= approx. rpm/9.55
m=mass of disk in kg
r=radius of disk in m
If we combine all this into one equation we get
E=1/4*m*r^2*w^2
Now for a given material the mass of a disk is
m=2*pi*r*t*p
t=thickness in m
p=density of material in kg/m^3
So substituting in m we get
E=1/2*pi*r^3*t*w^2*p
You can play around with this to solve for whatever you like.
However, you do run into several problems.
1. If you make the rotation speed too high and the disk radius too big than the disk will explode because the stress on it is too high.
2. You must have really good bearings and remove as many other sources of drag as possible to store the energy for any reasonable amount of time.
3. To store a reasonable amount of energy the disk will have to spin really, really fast.
Stepper motors can only achieve a speed of a few hundred rpm which is not fast enough to store a reasonable amount of energy. The ones that Parallax will also not be big enough to handle 400W of power. Stepper motors also have a fair amount of 'drag' or resistance to turning that will slow down your wheel very quickly.
Have a look at this page en.wikipedia.org/wiki/Flywheel_energy_storage
What causes the "drag" in the stepper motor?
I would assume that the rotor does not touch the stator.
Can you recommend a bigger stepper motor that can handle 400 watts max. during noon?
In your opinion, how should the stepper motor controller sync with the rotation of the flywheel?, or should I use a normal DC motor to turn the flywheel?
▔▔▔▔▔▔▔▔▔▔▔▔▔▔▔▔▔▔▔▔▔▔▔▔
www.fd.com.my
www.mercedes.com.my
I would use a brush-less motor because it is the most efficient. This should give 3 phase AC when being run as a generator which will need rectifying and conditioning.
Servos not only have the 'holding torque', but they are also geared.
▔▔▔▔▔▔▔▔▔▔▔▔▔▔▔▔▔▔▔▔▔▔▔▔
Don't visit my new website...
Now I am thinking that we should start small, maybe with a single 35w panel first, and use a small Parallax stepper and a small (about 5kg) iron flywheel.
Maybe a Hall sensor on the flywheel will help with the sync, so that the stepper would not mis-step.
There is no danger of mis-step when getting energy back, because the stepper is freewheeling at that time.
Just put a bridge rectifier on every stepper coil and you get back the DC ( with pulses ).
The tricky part is how to drive the coil (when charging the flywheel) when the rectifiers are still connected to each coil.....
Steven,
I think if the microcontroller were to apply a small driving current to the stepper coils in sync with the RPM of the flywheel, the stepper would present zero drag to the flywheel.
▔▔▔▔▔▔▔▔▔▔▔▔▔▔▔▔▔▔▔▔▔▔▔▔
www.fd.com.my
www.mercedes.com.my
I made a mistake before. The formula for the mass should have been
m=pi*r^2*p
which means that the final formula for energy should be
E=1/4*pi*r^4*t*w^2*p
I've done a graph for a steel disk of 5 kg and thickness of 10mm. This works out at a diameter of about 280mm.
In the graph RPM is on the x axis and energy stored (joules) is on the y axis.
If we run the disk at 9000 rpm than we would be storing about 25kJ. If we have a 1W load than this will provide power for 25,000seconds or 417 minutes or about 7 hours. However, if we halve the speed we will only get a quarter of the energy because of the w squared in the formula. Also, this doesn't take into account the efficiency of all the components but it is a good place to start.
Stepper motors will have trouble getting to these speeds but a brushed or brushless motor should have no problem.
Edit: forgot to attach the graph...
Are you sure the calculation is correct?
I am dissapointed.
1 watt load for 7 hours seems rather small compared to what a NS70 car battery can do.
Maybe we need a 10kg flywheel and 20,000 rpm.
How many coils does the brushless motor have? I am not familiar with brushless motors.
Would it be easy to extract the energy with the brushless motor?
▔▔▔▔▔▔▔▔▔▔▔▔▔▔▔▔▔▔▔▔▔▔▔▔
www.fd.com.my
www.mercedes.com.my
Not only will you lose the energy used in that step, but it can actually brake the flywheel, cause extra stress on the motor(coil/rotor pulling one way, the flywheel the other way), and in worst case, create a power-spike.
▔▔▔▔▔▔▔▔▔▔▔▔▔▔▔▔▔▔▔▔▔▔▔▔
Don't visit my new website...
▔▔▔▔▔▔▔▔▔▔▔▔▔▔▔▔▔▔▔▔▔▔▔▔
There's nothing like a new idea and a warm soldering iron.
For some more theory...
Like I said before, if we spin the flywheel too fast than it will explode. The stress in the flywheel is
stress=p*r^2*w^2
Now steel has a strength of anywhere from about 200MPa to 1000MPa. For what we are doing we want to take the low end of the range unless you know the strength of the steel. We also want to include a safety factor. So our allowable strength is 100MPa.
In the attached graph the red lines are the stress in kPa (want less than 100,000) and the blue lines are the energy in Joules. To get watt-hours simply divide the joules by 3600.
Taking the theory further.
combining the two equations
stress=p*r^2*w^2 and
4*E/(pi*r^2*t)=r^2*w^2*p
we get
4*E=pi*r^2*t*stress
E=pi*r^2*t*stress/4
but m=pi*r^2*t*p so
E=m/p*stress/4
So for stress=100MPa and m=20kg and p=7800kg/m^3
E=20/7,800*100,000,000/4=64kJ
See the second graph attached for different options. The x axis is mass in kg and the y axis is energy in joules.
I think there are also many types of steel.
Maybe if we use a few pieces of car disk brake rotors, bolted together, they might be stronger.
How many RPMs would the disk be spinning when the stress reaches 100 Mega Pascals?
Can the bearings take the RPMs and the weight?
▔▔▔▔▔▔▔▔▔▔▔▔▔▔▔▔▔▔▔▔▔▔▔▔
www.fd.com.my
www.mercedes.com.my
Disk brake rotors aren't a bad idea but I would check what their maximum speed is.
So more theory...
Using these two equations
E=1/4*m*r^2*w^2
E=m/p*stress/4
we get
1/4*m*r^2*w^2=m/p*stress/4
r^2*w^2=stress/p
w^2=stress/(p*r^2)
w=sqrt(stress/(p*r^2))
or for rpm
rpm=9.55*sqrt(stress/(p*r^2))
So the amount of energy you can store depends on the strength of your material, the density of the material and the mass of your disk. You can make the disk any radius you want so long but you will have to change the thickness to keep the same mass.
The speed depends on the strength of your material, the density of the material and the radius of your disk but NOT the mass.
So the design process is to
1. decide how much energy you need to store
2. choose a material for your flywheel. This will give you the allowable stress. Don't forget a safety factor of at least 2!
3. calculate the needed mass of the flywheel
4. choose a motor/generator. This will determine what speeds you can use.
5. from the speed and mass, calculate the radius and thickness
6. select appropriate bearings. This will be based on the mass of the flywheel and the required life the bearings
Steps 4 and 5 could be swapped if you have to fit the flywheel in a certain space.
Hope this helps.