OSU enters Mars Rover challenge with Parallax QuadRover
Hello Parallax Forum Readers,
Last Sunday four friends and I piled into a Ford 250 and left Corvallis, Oregon to visit Parallax Inc. in Sacramento, California. Our purpose for this 500 mile roadtrip was to pick up a QuadRover donation, so our club could enter the University Mars Rover Challenge. Through some amazing fortune and generosity we had been chosen as a test group for this new outdoor robotic platform.
The University Rover Challenge, URC, is a 2nd annual competition held at the Mars Desert Research Station, near Hanksville, Utah. There are 9 universities competing this year, from the East to the West Coast of the US. A school from Canada and another from Poland are also fielding a team. The competition this year will be an amazing experience.
The purpose of this thread is to give us a chance to report on the usability and features of the QuadRover. A Propeller chip will also be used extensively for this project as well. We will bring up problems we're having and invite you to ask us questions as well.
Here's a link to a youtube of the competition last year:
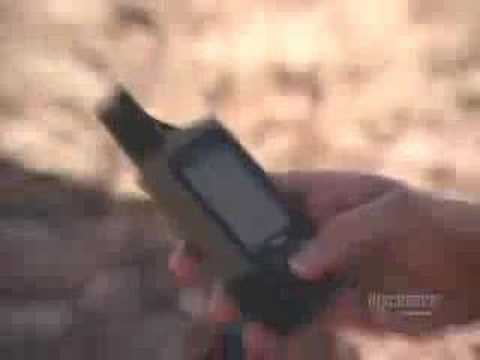
Here's a link for the URC:
http://www.marssociety.org/portal/c/urc
Thank you for this opportunity Parallax!
Matt Shuman
Oregon State University Robotics Club
Post Edited (Shuman (OSURC)) : 2/28/2008 6:33:08 PM GMT
Last Sunday four friends and I piled into a Ford 250 and left Corvallis, Oregon to visit Parallax Inc. in Sacramento, California. Our purpose for this 500 mile roadtrip was to pick up a QuadRover donation, so our club could enter the University Mars Rover Challenge. Through some amazing fortune and generosity we had been chosen as a test group for this new outdoor robotic platform.
The University Rover Challenge, URC, is a 2nd annual competition held at the Mars Desert Research Station, near Hanksville, Utah. There are 9 universities competing this year, from the East to the West Coast of the US. A school from Canada and another from Poland are also fielding a team. The competition this year will be an amazing experience.
The purpose of this thread is to give us a chance to report on the usability and features of the QuadRover. A Propeller chip will also be used extensively for this project as well. We will bring up problems we're having and invite you to ask us questions as well.
Here's a link to a youtube of the competition last year:
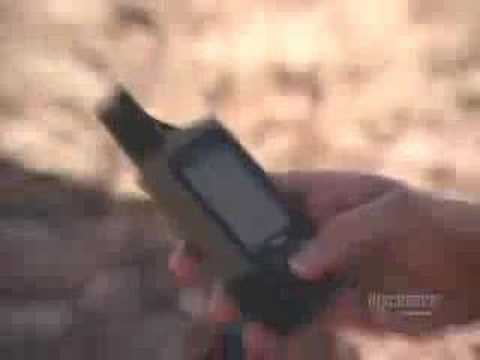
Here's a link for the URC:
http://www.marssociety.org/portal/c/urc
Thank you for this opportunity Parallax!
Matt Shuman
Oregon State University Robotics Club
Post Edited (Shuman (OSURC)) : 2/28/2008 6:33:08 PM GMT
Comments
▔▔▔▔▔▔▔▔▔▔▔▔▔▔▔▔▔▔▔▔▔▔▔▔
Whit+
"We keep moving forward, opening new doors, and doing new things, because we're curious and curiosity keeps leading us down new paths." - Walt Disney
So it turns out that the QuadRover uses four solenoids and three servos to control it:
A left motor enable solenoid
A left motor direction solenoid
A right motor enable solenoid
A right motor direction solenoid
A throttle server
A left brake servo
A right brake servo
The solenoids work off of 12 volts and draw about half an amp each, the servos work off of 5 volts and also draw about half an amp each at stall. So I needed to design a hefty 5v power supply and relay circuit so that the propeller could control all these parts.
Note this is only a prototype for right now so that we can get the rover up and running. Later designs will probably use solid state MOSFETs to control the relays, as they are more reliable. Oh and for those of you that can't wait to get their hands on one of these rovers, lucky for you guys I believe parallax is designing a control board that will be included with the rover.
Anyways I just wanted to share these pictures, so enjoy! Oh and if you were wondering on if it was hell to solder... it was... it took me about three hours of planning and soldering.
Feel free to ask questions and make comments, a circuit diagram will be available upon request.
This evening, I wanted to get it up and running and was quite successful. With the Propellers Object exchange and some debugging our new GPS module I was able to do most functions in about an hour. I was really surprised at the accuracy of the GPS module. It was basically able to pinpoint my couch where I was programming at the time.
This is really fun! The Propeller and its community are very helpful and inspiring, especially for someone new to "Spin", the higher level language of the Propeller.
-Ryan Albright
Oregon State University Robotics Club
Post Edited (Albright (OSURC)) : 3/8/2008 5:55:01 AM GMT
Sorry, I had to ask.
▔▔▔▔▔▔▔▔▔▔▔▔▔▔▔▔▔▔▔▔▔▔▔▔
OS-X: because making Unix user-friendly was easier than debugging Windows
links:
My band's website
Our album on the iTunes Music Store
Check these links out:
www.space.com/businesstechnology/technology/mars_gps_040707.html
www.msnbc.msn.com/id/5387135/
The future is always sneaking up on us.
-Ryan Albright
Post Edited (Albright (OSURC)) : 3/8/2008 8:27:10 AM GMT
Here are some pictures of the workstand that I built to keep everything organized in our mentor's garage. The shelves are great for storing the gas, motor oil, hydraulic fluid, and propeller development tools. The wheels are kept about an inch off of the table, which is great for testing the rover. It goes 14 mph, but I only go about 10, on a good day.
Some possible additions for this workspace would be a power strip and maybe a fold out leaf on the side. It's working pretty well so far though.
Matt
Ken Gracey
Here is an update of where we are.
We have succesfully gotten wireless communication to the Rover and controlled all motor functions through our data transceivers. Our work stand proved very useful in both keeping us safe and organized. We also were able to integrate both the Parallax GPS and Digital compass into our system and get very accurate information from them. Once we had movement, we needed to make sure that we had some sort of safety cutoff for the engine, so we moved the cutoff switch to a more optimal location and tethered a safety line to it. This will make sure that it doesnt try to run into anything unexpected. We will probably replace this with a more electrical solution eventually, but for now we want everything working.
We plan on having it on the ground in no time. We will make sure to post video of our first takeoff!!!
-Ryan Albright
Here is a block diagram to help explain the pictures in Ryan's prior post:
Wireless Transmission:
The beige box U-Bolted to the rover frame is a wireless transmitter that was found from a prior project at OSU. It automatically handles connection and maintenance of the communication channel. The specified link throughput is 115Kbaud, we have it set to 9.6Kbaud while testing it. Specified range is 20 miles, but we are very skeptical of that number. To test this, we took two of them and attached them to laptops running hyperterminal. Ryan stationed himself with a unit at the 7-11 while Jordan drove away with the other unit echoing results back to ryan. We found a more realistic range of 3 miles, but still better than our project requirements.
5 Volt regulators and Solenoid control Board:
Jordan's board is shown in the left side of FullPrototype1.JPG. The enable solenoids are enable hydraulic fluid through both motors by default, and the direction solenoids are default forward. For our first test we want the rover to use throttle and brake to move in the forward direction only, so we can stand behind it and be safe. That is why the 4 relays are disconnected from the solenoids.
The 5 volt regulators power the throttle and brake servos. Each servo can draw up to half an amp each, especially the brake servos, which is why we have multiple regulators for our system.
RS-232 to TTL converter
Our breadboarded converter is shown in the right side of FullPrototype1.JPG. We used TI's MAX232 chip and used the app notes for this block.
Safety Tether
Safety has been a concern of ours, both our safety and the quadrover's. We brainstormed about 10 different methods ensure that absolutely nothing could cause a loss of control, causing the rover to charge into something at 14 miles an hour. One problem we forcasted was a loss of power when the throttle is open. This would cause the propeller to reset and then rover would charge forward with no regard. Our solution is shown in KillSwitch.JPG. We had to rotate the switch 90 degrees clockwise, but this has given me confidence about our ability to stop the rover if need arises.
Next Step
Like Ryan says, we're going to have this roving pretty quick. Keep checking on us, and we'd love to get advice from this forum.
Matt Shuman
·
The moment·we all have been waiting for has just arrived... Our first video post of the rover driving! Today we were lucky enough to get a break in the rain so we went out with a video camera and took some video of our sweet QuadRover. I have posted the two best videos on YouTube·(links below) so go check them out! Please vote and comment, and if you’re a registered YouTube member subscribe to our channel and you will get notifications as soon as we post more videos. The first video is a demonstration of the rover, check out how easy it is to start! The second video is a test to see how well the QuadRover can climb over obstacles, that curb is just over half the size of the wheel, and look how easily it gets over it! Hope you guys enjoy these videos, if you want to see anything specific in the feature please let us know.
·
http://www.youtube.com/watch?v=4rEVZG1aGYM
http://www.youtube.com/watch?v=fyoPwR8uw80
·
Jordan
...Tiger
Sorry about the lack of new posts, we have been on Spring Break and have each taken a major task to complete. One task that has been breathing down our necks and really needing to get resolved was creating a Robotic Arm. I am fortunate enough to have worked at All Star Machine Inc the past few summers developing Surveillance Equipment and learned how to operate all sorts of sheet metal and machining tools. I decided to make our brackets out of 16 gauge Aluminum because it is light but strong enough for our application.
Speaking of which what we need to do is be able to attach a 1/2 inch hex bolt to a control panel from 15 to 75cm off of the ground and at up to 45 degrees off of horizontal. With that said, we decided to use a GatorGrip socket which will grab onto a bolt that is between 1/4 and 3/4 inch. This should give us a little bit of play in our control scheme.
So I needed to design a good set of interchangeable brackets that would let us make an arm perfect for our application. I first drew up everything in Solidworks and made a model of everything to make sure that everything would work exactly the way we wanted it to. Then I made flat models and got some help making a program for the AMADA punch at work. Five minutes and 500+ hits later, all of my parts were punched. Next I used the brake press to form them to spec. Then I machined our square tubing to be perfectly to spec and at multiple sizes. I made 4, 6, and 8 inch segments for easy and interchangeable repositioning. To attach my brackets to my segments, I used 3/8 stainless steel pop rivets (Overkill you might ask, maybe; Awesome, definately!).
I also machined a attachment for our GatorGrip to easily fit a servo head.
Check out these pics and I would love feedback!
-Ryan Albright
Good news! We have the rover driving around wireless with our new control system and we have video of it!!
Oh and did you know that the QuadRover can pop wheelies!? Well it can, go check it out in the cool new videos.
Jordan
▔▔▔▔▔▔▔▔▔▔▔▔▔▔▔▔▔▔▔▔▔▔▔▔
Whit+
"We keep moving forward, opening new doors, and doing new things, because we're curious and curiosity keeps leading us down new paths." - Walt Disney
Keep up the good work!
Paul
Work on the control for the robotic arm has gone well. We're going to use some telerobotics to control the robotics for this project. We're going to make a controller arm for the control tent that mimics the rover controller arm. The controller will move the controlling arm and the distant robotic arm will mime the actions. Our AX-12 servos were back ordered and will take about another 7 days to arrive, but we'll be ready for them.
Attached is the schematic and picture of this setup.
There's also a YouTube posted:
Matt
...John
P.S. I'm attaching a freeware terminal program that I "think" might work in windows. Think you'll like it if it works. It's petty nice for hardware debugging.
Here's what's going on. The gasoline engine drives a generator, the generator charges the batteries, and the batteries drive the electric motors - I THINK!
I understand there are hydraulics on it too, but I'm not sure where they fit in.
Regards,
Bruce Bates
▔▔▔▔▔▔▔▔▔▔▔▔▔▔▔▔▔▔▔▔▔▔▔▔
Involvement and committment can be best understood by looking at a plate of ham and eggs. The chicken was involved, but the pig was committed. ANON
So here's the scoop on the QuadRover. The gasoline engine drives a hydraulic compressor. We can then open, close or reverse solenoid valves to control the flow of fluid through the motors. The default power system for the electronics is a separate 12 volt lead acid battery. There is no generator to recharge the battery while being operated. The fuel tank size .8 qt, so the battery will last longer the gasoline.
Matt
I've been working on assembling the robotic arm for the rover this past week. Here's a link to a video that shows our concept. We're going to finish assembling the arm this weekend, and it should be turning bolts by Saturday. It's really fun to operate and we're excited to start getting some interesting videos posted on this forum. Let us know if there are any features or questions that you'd like us to talk about or photograph for you.
Video of the arm moving with a controlling manipulative:
Matt
So I have made a lot of progress on my Propeller Protoboard that I am designing and I wanted to share my design with you. I have completely done away with the relay control board that I posted on this forum a while back. All solenoid controls and 5v supply are now implemented on the Propeller Protoboard. Instead of using unreliable relays to control the solenoids I am now using some low side power MOSFETs (Digikey part#: BTS133IN-ND) These MOSFETs are great for controlling the solenoids on the QuadRover as they have a very low on resistance and have no problem being driven by 3.3v from the Propeller. Our Propeller Protoboard design also has an RS232 level converter and headers to plug in GPS, digital compass, solenoids, wheel encoders, and servos.
Take a look at the picture, its looking very cool!
Jordan
Chuck
Here at OSU, we have recently acquired a 3D Printer, which has proven to be an invaluable asset to this project. All I have to do is Solidworks up a model, and click print, and an hour or so later, there is my part. NO machining necessary. While machining a part would be stronger and better in the long run, I dont have access to a machine shop to work while Im down here at school. SO t his printer has been awesome.
I was hoping to have all of these parts up to show everyone by today, but the printer had encountered some technical difficulties and is currently getting maintenance. So ill show you the solids that I drew up in SW instead for now.
Camera Servo Mount: This is used to mount our point and click camera to an AX-12 servo mount
Futaba Back Plate: This is so that we can mount an AX-12 bracket to a standard Futaba Servo for tilting a camera.
Robo Arm Attach: This is a wrench which is lighter than the GatorGrip. We want to test and see if having less torque on the end of our arm will prove valuable
Encoder Mount: For GPS waypoint navigation, we wanted some form of distance detection, we will moniter the disk brakes ventilation holes.
Soil Sensor Arm Attach: This is so that we can mount a Spade Bit and a PH/water concentration sensor to a servo for 180 degree turns
Also, we are using a spade bit with thermocouple to get temperature measurements at 10cm below the surface and after drilling the hole, we are going to insert the PH/soil sensor in the hole and take the rest of our measurements.
Ryan
We've made some progress on the robotic arm. Here is a photo and youtube link for our construction task.
The books are used to get the robotic arm 9 inches above the ground, modeling the height of our rover mount location.
Matt
Here is our latest version of the soil testing attachment. One side is a spade bit with an attached thermocouple. This allows us to drill 10 cm into hard clay while measuring the soil temperature. The other side has a probe that measures the soil pH and moisture. One major drawback is that we can not measure the pH of dry soil with this current setup.
Matt
I recently made some wheel encoders for the Quadrover utilizing the ventilation portion of the ventilated disk brakes. Turns out that the holes in the brakes make excellent wheel encoders when paired with a photo-interrupter. Ive attached a picture of the 3D printed encoder housing mounted around the disk brake using the brakes same mounting holes. All I have to do is press in the photo gate, and presto... the ideal wheel encoder. One of these encoders is on each brake and will give us good velocity and distance information. We calculated that these will trigger about every 3/4 of an inch so we can be fairly confident that this will give us very measurable data