Compass Module 3-Axis HMC5883L problems and more.
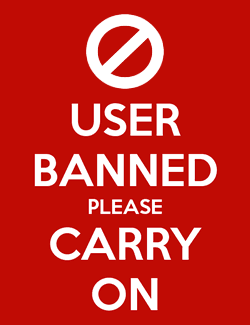
in Accessories
I was testing the HMGC5883L sensor among others on an AB WX. Everything bought new -unused.
Any power supply; multimeter; proto-board and whatever else used during the tests are OK.
Software was downloaded from the KickStart examples.
The first problem began losing the 3.3v rail on the AB WX board leaving it useless.
Next test was done using same sensor with a Propeller Mini and a bench power supply noticing, just after running the program, a drop in the power supply from 3.3v to less than 2.5v (at Vin, not at SDA/SCL) and 3.3v OK while doing nothing.
Disconnected from Propeller Mini and applied 5v to sensors Vin the HMC5883L IC “smoked” immediately. Power requirements for this sensor: 2.7 v to 6.5 v.
The resistance measured after that at Vin-GND was 5 ohms. After heating a bit the FAN2500S25X sensor´s regulator, resistance went up to 180 ohms -due its thermal sense or thermal compensation- and finally reaching down 110 ohms at ambient temp.
The FAN2500S25X is a fixed 2.5v reg.
Appling 2.7v at sensor´s Vin the reg.´s Vout was a bit more than 2.5v.
Appling 2.9v at sensor´s Vin the reg.´s Vout was a bit more than 2.7v!!!
Appling 3v at sensor´s Vin the reg.´s Vout was a bit more than 2.9v!!!
So at 5v?????
This means the sensor´s reg. is fried and when I had applied 5v to the sensor, it went over the ABSOLUTE MAX Vdd for the HMC5883L IC (4.8v), burning it.
After a close inspection of this sensor using a powerful magnifier, I saw LOTS of very little lead balls stuck between the components and board.
The same found on the AB WX board but bigger, especially under the caps and the bottom side of the board but that was not the real problem on the AB WX! A white paste was left, most of it all around the regulators zone. That paste turned greasy and hard to take it off. Under the zone in which paste was applied, some tracks darkened same around schottkys cathode pad.
The sensor triggered the problem on the AB WX board.
The board is working back without pulling a component but this means the board eventually will damage when copper of those darkened tracks decompose. Electro mechanical migration and moisture sensitivity level are two points to take in consideration when manufacturing.
Things happens and this was my turn.
EOF.
Any power supply; multimeter; proto-board and whatever else used during the tests are OK.
Software was downloaded from the KickStart examples.
The first problem began losing the 3.3v rail on the AB WX board leaving it useless.
Next test was done using same sensor with a Propeller Mini and a bench power supply noticing, just after running the program, a drop in the power supply from 3.3v to less than 2.5v (at Vin, not at SDA/SCL) and 3.3v OK while doing nothing.
Disconnected from Propeller Mini and applied 5v to sensors Vin the HMC5883L IC “smoked” immediately. Power requirements for this sensor: 2.7 v to 6.5 v.
The resistance measured after that at Vin-GND was 5 ohms. After heating a bit the FAN2500S25X sensor´s regulator, resistance went up to 180 ohms -due its thermal sense or thermal compensation- and finally reaching down 110 ohms at ambient temp.
The FAN2500S25X is a fixed 2.5v reg.
Appling 2.7v at sensor´s Vin the reg.´s Vout was a bit more than 2.5v.
Appling 2.9v at sensor´s Vin the reg.´s Vout was a bit more than 2.7v!!!
Appling 3v at sensor´s Vin the reg.´s Vout was a bit more than 2.9v!!!
So at 5v?????
This means the sensor´s reg. is fried and when I had applied 5v to the sensor, it went over the ABSOLUTE MAX Vdd for the HMC5883L IC (4.8v), burning it.
After a close inspection of this sensor using a powerful magnifier, I saw LOTS of very little lead balls stuck between the components and board.
The same found on the AB WX board but bigger, especially under the caps and the bottom side of the board but that was not the real problem on the AB WX! A white paste was left, most of it all around the regulators zone. That paste turned greasy and hard to take it off. Under the zone in which paste was applied, some tracks darkened same around schottkys cathode pad.
The sensor triggered the problem on the AB WX board.
The board is working back without pulling a component but this means the board eventually will damage when copper of those darkened tracks decompose. Electro mechanical migration and moisture sensitivity level are two points to take in consideration when manufacturing.
Things happens and this was my turn.
EOF.
Comments
For the AB WX board, yes, I had taken some pictures of the leads balls still there even after many touching; cleaning and movement. Need to reduce in size to post. Let me try.
What type power supply did you use to power the PAB WX?
All tests were done without load, only a multimeter. So until now can´t confirm any deterioration or damage to components.
There are 4 MOSFETs controlling USB power reg. and V_aux. on/off but not shown in those pictures,
The supply was just the USB port and confirmed to be OK. After the lost of 3.3v rail I connected a battery holder with 5 rechargeable bats. so close to 7 v. Only the first time the batteries were connected, the 3.3 v were measured again not anymore. During test: USB ports; the bat. holder; a powered USB hub and a MICROCHIP wall wart used for my development boards, so it is also working and OK.
The SERIOUS problem started once the paste melted, perhaps after the bad sensor pulled too much current (the paste acts the same under cool conditions). That´s why I mention electro-mechanical migration, And depends on soldering process, small lead pellets can be left around joining the paste. I´ll try to explain the best I can.
The cap. connected to the 3.3v reg.´s Bootstrap (BST) had a very low impedance, to be precise, a very low resistance, I haven´t pulled the cap. just measured with an ohm meter.
The 3.3 reg. same as the 5v reg. are short circuit protected but BST must be over reg.´s Vout or VLX. With that shorted cap., impossible. It also put the coil´s freewheel schottky to BST. BST is a delayed startup LDO so Low Differential voltage is needed but not zero, that´s why this reg. is a buck reg. and not a real DC-DC one. Under this conditions reg. will never start up.
After removing a bit the greasy paste, and noticed the dark spots on the board something happened when the tip of the ohm meter touched the side of the schottky, and yes, I mean the plastic capsule, It shown a resistance to gnd so indeed a current leakage (moisture sensitivity level). If this is happening, the value of the resistances to set the output voltage, also could changes.
Everything was pointing to problems with the paste so I get the MacGiver´s toolbox, took the most ultra sophisticated tool, a very sharp toothpick; absorbent paper a needle and alcohol.
In 5 days of cleaning around the BST cap. the resistance went from 15 to more than 2M ohms. It´s not organic and it can´t auto-heals.
The MLLC cap. is like a microscopic sponge. Things get worst if any compound around them have some common salt (perhaps any other salt makes similar effects), as part of the cleaning solutions. I´m not saying this is the case cause I don´t know the formula but the palladium associates to NaCl quickly. In the presence of current, so some electrons running around, the Cl- gets free and populates the interstices of the ceramic. Cl- is also free in current water.
Ok enough bla bla, just to finishing with this cap. In that conditions the cap will drain a lot of current at low voltage. If applying a bigger voltage to cap. with migration problems, the current must fall down abruptly confirming the migration.
I really don´t doubt on that mosfets, and power control is working good. The last was that USB can put the 3.3 v to the board even if FTDI 3.3v out was 3.31v, but only after further cleaning with my "specialized tools" and cleaning the cap with the lead ball shown in picture that board seems to be OK. Also the biggest cap close to the A/V jack was hosting this lead balls!
Not sure what will happens when I put some load to the board but I´m afraid to leave this things unattended, I mean the board and any sensor separated or all together, could burn anything without notice.
EOF.