My First ExpressPCB order... help review please!
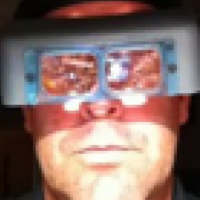
.
If you remember a while back I was working on a Keypad Decoder, the Hard Way. Well thanks for all the help then. Especially Beau Schwabe for the simplification of the design. Well with some time on my hands for the Holidays, I finally got around to laying out a PCB and it has taken me a day or two to get to this point.
I added an 8 bit I/O expander to reduced the Pin usage to just 2 pins. I'm pleased with the result now and think I am ready to order prototype boards.
Here are the Schematic and PCB images. Please advise on what I may have screwed up or could maybe could have done better.
Thanks!
Paul
Schematic:
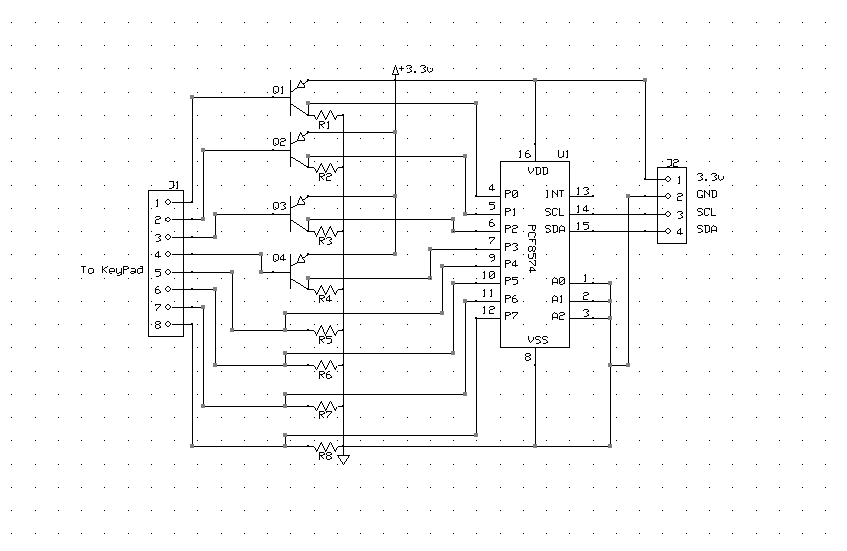
PCB:
If you remember a while back I was working on a Keypad Decoder, the Hard Way. Well thanks for all the help then. Especially Beau Schwabe for the simplification of the design. Well with some time on my hands for the Holidays, I finally got around to laying out a PCB and it has taken me a day or two to get to this point.

I added an 8 bit I/O expander to reduced the Pin usage to just 2 pins. I'm pleased with the result now and think I am ready to order prototype boards.
Here are the Schematic and PCB images. Please advise on what I may have screwed up or could maybe could have done better.
Thanks!
Paul
Schematic:
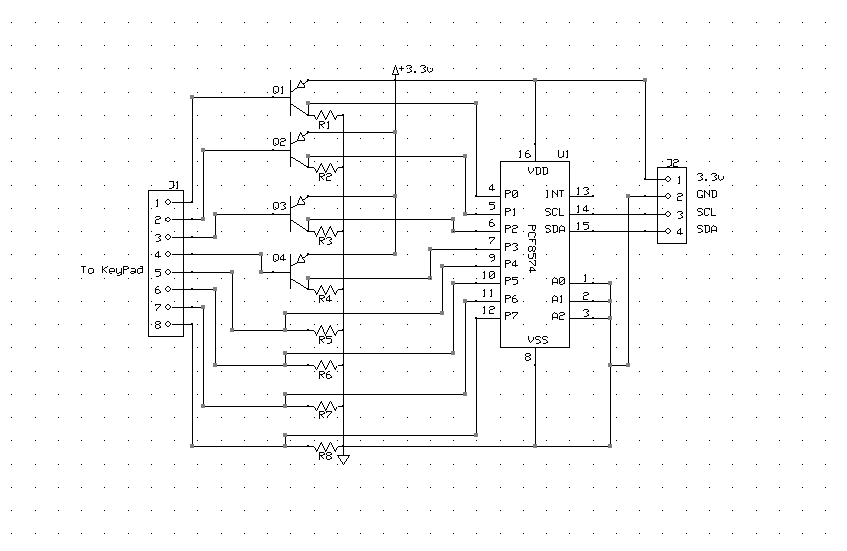
PCB:

Comments
Apparently right angles are looked down on for PBC layouts. They can cause problems with high speed signals and I've been told they don't etch as well as 45 degree angle turns.
The way the traces meet the holes for R2 and R3 aren't dead on. Again, I've been told these can cause etch problems (acid traps is what I've been told).
Hopefully someone with really experience will chime in.
And thanks for the tips!
Decoupling capacitor(s)?
The right-angle thing matters for GHz speeds on stripline, less important at lower speeds, but 45 deg angles look
much more professional
Thin traces fine for logic - reduces crosstalk in fact when over a groundplane. thick traces for supply between
chips and decoupling capacitors at least.
Thanks for the tips!
Here's a new version:
FF
Thanks everyone!
Paul
It looks like you can also make this a one layer board by routing between the pins of the IC. This is a choice of yours, but I would prefer minimizing the number of layers.
You might also want to consider adding mounting holes, along with the previously mentioned informational text.
You can make the board smaller (and, hence, possibly cheaper) by moving R5-R8 up to a more compact position.
If you really want to shrink the thing, go surface mount. Transistors and 0612 format resistors and caps are easy to do with fine tip. Also the ic may be available in soic so even that is doable without much effort. Possibly reduce the cost with fewer through holes to drill/plate etc.
Surely that's "you must add 0.1uF decoupling cap next to the IC". No logic chips are guaranteed to work (reliably) without proper supply decoupling.
Just run that top trace all the way to the IC pin on the top side.
And as others have pointed out, get a decoupling cap on that IC.
Bean
Also, when using ground planes, keep an eye on the width of the copper plane between traces, such as you have above your parts labeled Q's. For example, if you were to expand the width of those traces, there's a possibility of the copper plane between those traces getting unacceptably thin, which could cause the ground plane there to peel off and cause shorts. I don't think you're in any danger of that now, but it's just something to watch out for if you make changes.
Merry Christmas, Santa
A couple of you have mentioned making the board smaller to save cost - the ExpressPCB mini board service is a fixed size for a flat rate - so I've got room to spare on this one.
Here's the latest improvements you all have so graciously helped with.
traVis.
I would think having a ground plane helps to protect a non-RF circuit board from interference from the environment, at least somewhat. I seem to remember a circuit I had with a real time clock (RTC) getting reset due to a device in the same room that would do some fancy inductive loading now and then. The addition of a ground plane seemed to solve the problem, and since then, I've been using ground planes as an RFI preventative measure for many of my circuits. Have I been wasting my time with ground planes? Do they not help in holding down some RFI? Hey, if nothing else, shiny ground planes look better than those dull boards you get with the miniboard option. Adding a ground plane makes the PCB look like you almost know what you're doing sometimes. No?