Soldering SMD boards at home - hints please?
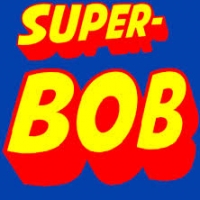
A ham radio friend of mine experiments quite a bit with DSPIC microcontrollers and audio codecs to make software defined radios. Latterly the best parts only come in leadless packages. He's interested in any advice on DIY soldering boards populated with these devices, please. How successful have you been and with what equipment?
Comments
Some success with Very Fine point soldering tips on Weller stations. Any type of air pen works much better for non-touch soldering of SMDs. My first air pen was a homebuilt job using a radio shack desoldering tool with an aquarium pump for air flow, and it did pretty well. Next at work was an Ayoui brand of air handle (way to big to call it a pen) with soldering iron station in a big black box. Not bad, but too big and not the greatest air control. Was pretty good for salvaging parts for experimenting when a board was getting tossed out.
Currently working on a Zephyrtronics setup. Work has a way of getting in the way of fun, but it does pay for toys. Stay away from the Zephyrtronics on ebay, at least as far as the air pens go. The priciest part of repair is the pen itself, so by the time you add the ebay price to the cost of repair, you may be close enough to new or guaranteed working resale to just go that way. Same goes for the Airbath. As to the pick pen, you could buy a handle from many places that will work as well, or ebay it with new rubber hose and a likely good handle. Solder paste is a must with air or a dead steady hand for soldering iron. If I am not absolutely steady, I end up pushing the part off the pad at times with a shake or two at the wrong time. Air is much better. There are a ton of utube videos that are pretty good including some that Zephyrtronics has out. Problem with paste is it comes in syringes, and they are a pain to hand dispense. I just got a screw type device on amazon that seems to do a nice job of putting down a uniform line across the pads and small dots without to much excess if I back off the pressure somewhat like the dripless caulking guns. Have some fine solder wick in case of bridges.
Last thing, PRACTICE before attacking a pricey board/part. There are a number of practice kits for pretty cheap prices on amazon for training and practice. And they do stuff like flash leds etc so you know you did it right. oh, before I forget, get a good pair of loupes for working on this stuff. Over ^0 yo eyes, need a bit of magnification. The surgical/dental loupes are getting cheaper these days; get a set of Croakies (or whatever they are called these days) to keep them in place on your face, it gets very annoying to try to keep the eyepieces from sliding down the nose at just the wrong time.......
I use an infrared toaster oven and Zephpaste. As long as the board isn't too big, it works great. Large boards can be a problem due to inconsistent heating over the surface, since my oven lacks a fan. A convection oven would work much better.
I typically use the Zephpaste syringe with a very fine tip to dispense the solder, one pad at a time. For semi-production runs, I make a pastemask on my laser cutter from Kapton film. Then I can squeegee paste onto multiple pads at once.
For the few inevitable solder bridges that occur, solder braid does the trick for me.
BTW, Zephpaste is the only solder paste that I've had any success with. Kester was easily the worst. Zephpaste has an amazing shelf life, and the solder particles are super-fine. I keep it in the fridge when I'm not using it and let it warm to room temperature before dispensing.
-Phil
All my PCBA builds at home are done with:
I have done µBGAs, QFNs, and numerous other components most people would not normally do at home with this process. Every one of my ~800 PowerTwigs, most of my M44D40s, all of my SHT15 boards, and one of my PropBSC prototypes were done with this setup.
While I disagree with Phil's opinion about Kester, I would second his recommendation for Zephpaste. It is very forgiving for DIY environments due to the higher than average flux content. My only issue with it is the price. At ~$25 for a 12 gram syringe, it seems crazy compared to 500 grams of Kester EP256 for ~$100. In either case, the solderpastes work well WAY past their posted shelf life, so don't be afraid to buy more than you would use in 6 months. A Kester engineer told me years ago that they have had customers validate solderpastes more than 8 years old with results equal to fresh paste. The shelf life is just where they "guarantee" the paste's performance. Nothing sinister occurs on day 181, LOL.
My process:
I use this Alpha solder which has lead, much preferred to no-lead.
https://www.hisco.com/Product/151952-1998
One lesson is, keep in the refrigerator at all times. Take out of the tube what you think you need for that board, warm up the solder you removed with a heat shrink gun so it is easier to flow in the screen but don't overheat and cause it to melt. Don't try to re-tube solder. Trash it or store it for disposal. Keep the solder syringe pushed out so there is the least amount of air in the tube. Air and warm temps reduce the life dramatically. RE-tubing cuts the life and makes for bad solder joints you need to repair later. Many lost hours fixing boards with solder that was re-tubed after squeegy-ing and scraping up to save.
https://www.neodensmt.com/reflow-oven/neoden-t-962a-small-mini-reflow-oven.html
I have used this 962 oven tons over a few years. Works great. Just press Go, no programming. You can get cheap Convection type ovens to work as well but you have to manually enter temperature to create a profile, which gets old fast if you are making boards often. You can insert a thermocouple probe into the oven and connect it to a voltmeter to help create your times and temps for your profile.
https://www.stentech.com/
I have ordered many stainless framed stencils from stentech over the years. Same day ship in most cases when they receive files and approve the art. 5mill stainless works well for most types of parts. I used to make Kapton mylar type stencils with a laser but only for a one off cases, the heat from the laser melts the mylar at the cutouts and can raise the material off the board some where it is raised, which allows solder to bleed under. Not a big deal but something to pay attention to. Make one clean pass with a hard edge ie flat stainless solder squeegie. Don't make multiple passes over fine detail parts.
To repair bad connections on pins you need a cheap 75$ or so air rework tool and some type of flux liquid or paste to help make seating parts go much easier. Electrostatic cleaners can be great using alcohol for the first pass then windex to remove the alcohol/water white residue. Harbor freight Electrostatic is around 75$ and works great on boards.
I make boards on Eagle, then upload files to 4pcb.com only using their 33$ special boards. Minimum 3 boards required. I put as many boards as I can fit on a 10" x 6" or max 60" on a "panel" for the lowest per square inch price. They do add a fee for multiple boards images on the panel, not a big deal. Also hit you with shipping and handling fee. Still cheap. 3 day turn around. Rock solid company, made thousands of board with them rarely an issue. I would never a couple of boards for example 2" x 3" with this process, only fit as much as possible on 60" square inch area. There are other companies with their own software that makes it easy to make boards and upload. Find one that you prefer.
Invest in some high quality stainless tweezers like this
https://www.mcmaster.com/5669A13/
A lighted magnifying glass on an adjustable arm is a must.
I engrave the Kapton cutouts. With the right laser setting, I don't get the melty effect at the edges. It takes several tries to get it right.
-Phil
Many thanks for the tips, chaps, very useful!
I built my own reflow oven out of a toaster oven like @"Phil Pilgrim" mentioned. I used this kit -
https://www.whizoo.com/controleo3 and it came out nice.
It works great. I thought I had posted some pictures about it in the past but a quick search came up with nil.
Paul
EDIT: I'll look for the pics and post if I can find them.
All good advice. The first thing I would say is to avoid the leadless (QFN) packages if you can for at home prototype work. Okay, I know you said that is what he wants to do. But that takes the task to another level. Unlike the nicely visible pins on a QFP package, pins that you can inspect, probe, and repair, with QFN most of that is hidden underneath, visible only to x-rays, indirect functional testing, guesswork and cussword repair. Expect a higher failure rate, period. (until you become experienced
)
I'd recommend getting a stainless steel stencil in any case. The price unframed from Osh Stencils is low enough these days, not that much more than Kapton. I feel that they are that much better, especially if you are doing multiple runs.
I have a Zephytronics system too, and concur about it and about Zeph paste. My other heavy artillery is a Metcal soldering station with a wide assortment of tips. I wish though I had better eyes and a steadier hand!
A chip recently that stymied me was a 32kHz mems oscillator in a CSP (chip scale package), SiT1552, kind of a ball-grid, but only 4 balls. What could be so difficult about that? Well, a 1.8mm x 0.8mm package, with far more exacting alignment requirements than I could hope to achieve. A breath blows it away. Blink, it's gone forever. Success rate, one in 10. It's appeal was a +/-10ppm TCXO spec over industrial temperature while operating on 1µA power. Not to be for me unless I contract it out, and even then?
Tracy,
Thanks for mentioning Osh Stencils. I'd never heard of them, but their prices for stainless steel stencils are really attractive. I'm definitely going to be ordering one soon.
On a slightly different topic, does anyone here do lead-free hand soldering? I bought a high-temp tip for my Weller soldering iron. It works okay, but keeping it tinned has been a huge struggle. The tin/silver/copper-based solder I'm using just won't stay on the tip, and it's really slowing down production. Any hints would be appreciated.
OTOH, the lead-free Zeph paste I bought works great for SMT parts. No real difference from soldering with their leaded stuff.
-Phil
Actually, I find QFNs a breeze to work with, the 0.5 mm pitch preferred, of course, over 0.4 mm pitch ones - no bent/broken/missing pins and with the right amount of solder paste all is good and the chip just sort of jumps in to the right position by itself. BGAs I have no experience with (it's a "do not touch" attitude). The same goes for the (WL)CSPs. These are a no go for hobby use and home equipment for me. And fixing a broken/missing pin on a 0.5 mm pitch QFP chip is not that easy too from my experience. Doable, but not easy at all.
I (re)did a BGA on a consumer video product that had tanked. I figured “why not/maybe I’ll learn something”. The first attempt (a simple reflow) broke it even more. The next attempt I pulled the chip and used a reballing rig and all the “right” tools. Nope. Third attempt used ChipQuik rework paste applied with a tiny brush. That brought no joy either, and since the assembly/disassembly/assembly part was getting really old, into the bin it went.
So I did indeed learn something: “I dont mess with BGA’s”. 🤣 And I have a very nice, mostly useless, reballing jig to frame and hang on the wall to remind me of that fact.
Phil,
My lead-free tip tip is to apply plenty of flux. Have you checked out https://www.ameritronics.com/solderingtips.htm? Ameritronics is Zephyrtronics' parent site, with a wider product offeriing. That's where I find the tips for my MetCal MX.
@Maciek, To jump into place you have to be talking about the surface tension of PbSn solder!
I have had some success with QFN, not all doom and gloom. After beginner's luck, that yet comes once the footprint and the solder stencil apertures are resolved with the manufacturer's recommendations. Apertures for big center pads take special care. Then the squeegee action has to be impeccable and through a clean stencil, no underflow. Perfect, and then place the component without smearing the paste. It is a great relief when it does work well, a beautiful professional look.
Still, I prefer the pins, and another reason has to do with analog functions. It's much easier to clean out flux residue from between the visible QFP pins than it is from under the QFN body. Especially important with water based (conductive) flux. Residue can wreak havoc for high impedance inputs.
One thing I do with the few leadless parts I use is to extend the pads away from the package a tiny bit, beyond the manufacturer's recommendation. That way, I've got half a chance to see if a good joint has been made. So far, I've been pretty lucky -- even with paste deposited by a syringe.
Just don't overdo it, else package self-centering could be affected.
-Phil
IF you extend the pads out away from the pin then you also gain the advantage of using flux and fine time solder pencil to draw out a solder bridge or add solder to the side of the part and let it run in. But I find that QFN is easy with practice and even when pins to connect well, just use hot air tool and flux and usually its just a few minutes to life the part and replace it, extra flux making things fall in place better.