QFN chip solder points on both bottom and edges?
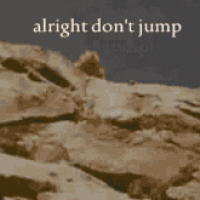
http://www.parallax.com/Store/Microcontrollers/PropellerChips/tabid/142/CategoryID/18/List/0/SortField/0/Level/a/ProductID/333/Default.aspx
The datasheet seems to imply both?
http://www.parallax.com/Portals/0/Downloads/docs/prod/prop/Propeller-P8X32A-Datasheet-v1.4.0.pdf#page=35
Does the QFN chip have solder points on just the bottom side, just the sides, or both?
The datasheet seems to imply both?
http://www.parallax.com/Portals/0/Downloads/docs/prod/prop/Propeller-P8X32A-Datasheet-v1.4.0.pdf#page=35
Does the QFN chip have solder points on just the bottom side, just the sides, or both?
Comments
For manual assembly, it can help to extend the PCB solder pads a little.
QFN packages also usually require the centre GND area, is soldered, and I think that is a stress cycling issue.
The center pad is not connected to chip ground, nor to any other electrical point, however, it is close to the chip substrate and should be grounded for best noise immunity. It is a mainly a thermal pad. Observe that there is also a tiny dot that pokes through near pin 1, and that connects to the central pad.
The C-3 board looks like it used the QFP as did the TetraProp
Added note:
Just saw the EEV blog on reflowing a QFN. He appeared to struggle a bit getting the paste laid down. Yep, it is a pain on a cold board. One trick I found for getting around this was to slightly pre-heat the board where the paste should be and the bead would kinda melt a bit and stick in place so it was not necessary to chase the paste around. The other thing that is a bit awkward is the paste will tend to "self-dispense" a bit after you release pressure on the plunger so you need to anticipate that effect just short of the end of your run.
Oh, the air pen I used to do this ( not EEV's blog video) was the infamous Radio Shack De-soldering tool with the aquarium air pump for the air supply.......
It worked surprisingly well!
Sometimes for hand soldering you can place some vias under the centrepad and a small amount of solder paste. Then after the outer pads have been done the vias can be heated to reflow the center pad. Be careful not to add too much solder as when squashed by the chip placement it may ooze out and create a short. Maybe slightly larger pad holes might be better.
For the thermal pad you can have very fine thermal vias through the pcb or even just normal vias and don't be afraid to flux the other side of the board and get the solder flowing. The package can actually withstand a fair bit of heat so give it a go. I do this with my L6470 stepper chips which most definitely need it.
A few processes were originally used to manufacture QFNs and the main difference was if the plating occurring before or after the component was removed from the lead frame, but the lead frame design is also a factor. In the case of Parallax's QFN, it has a standard QFN lead-frame that would create end terminals, but it is removed from the lead frame after plating. Hence, the end terminals cannot be considered a solderable terminal. However, with aggressive fluxes, the oxidation that will occur to these end terminals can be overcome and wetting will be accomplished. This can be seen in Tracy's third photo where some leads did wet and others did not.
As for the variations in pad design, it is becoming more common for QFN layouts to include extended length pads to accommodate some typical rework techniques. Reflowing the solder at the end of the pad can in fact reflow the solder under the part. However, this is not to be taken as a basis that handsoldering a QFN is always possible.
Exactly what I wanted to see. Thank you Tracy Allen, nice macro shot too....
So, although its difficult, a QFN footprint that has no slug solder points, and extended leg pads, would allow someone to rework/remove this chip if needed.
At first I was enthusiastic about the QFN package, partly because I had been using the SX48/BS2pe, and the Prop QFN takes about the same area on a circuit board. The Prop QFP is much larger. However... there were problems that were hard to resolve in short run manufacturing. On the other hand, QFP has its pins out where I can see them and get at them, and there is no question of how to deal with the center pad or matching of thermal expansion coefficients. It is much easier to clean too, which is a good thing for residual interpin resistance. So it's QFP for me now. That goes for other chips too. If I see a tiny DFN but the same thing is available in the msop with real legs, even though larger, that's what I'll choose.
Another advantage the QFP package has is the ability to route traces under the chip. When I was attempting a very small Propeller board, I found it was easier to make the board small with the QFP than with the QFN package. The area under the chip of the QFP not only allows traces but vias for lines which would have been otherwise blocked.
What sort of problems did you encounter? On Monday I'll be receiving my board that has a number of QFP chips, including the Propeller. Three of them I've been able to successfully solder on previous runs using a stainless steel step stencil (3 mil for the QFP chips), but I haven't tried the Propeller yet.
From the previous chips I discovered the key was the stencil. Using the high quality step stencil ($150) gave perfect paste deposition for all the pins, and I was able to achieve near 100% pass rate of the first try. Before, when I did hand paste deposit using a syringe I had a much lower success rate and had to do extensive rework.
Cody, what exactly is a step stencil? When I've done the QFNs in house, I've used kapton stencils from ohararp, or from pcbunlimited (UV laser, cleaner edges). I use 63/37 zephpaste. The first few boards come out fine, but then the paste starts to work its way under the stencil. I think that has to do with a combination of the temperature of the paste and also with it becoming fluidized as it is worked on the squeegee. The boards need a good marks to show how to place the chips, and that can be a problem if the paste spreads out. Particularly with small DFNs where you don't have a square to center into. I use a binocular microscope to check alignment before reflow. Board and chips have to be very clean to start with. I'd say most problems are lack of connection to a pad, hardly ever short circuits. That is with 63/37 solder. Lead-free is much harder, due to the low surface tension to help pull the chips into alignment. And rework is harder for the same reason. I contract out the lead-free work, and that is usually runs of up to 300 boards. The problems there have been few and far between, but when they occur it is usually lack of connection to a pad. I think the large beads on the ends of my pads indicates that the openings in my stencil are a bit larger than they need to be.
Thanks, that helps.
A step stencil is one in which the thickness of the stencil is another parameter that you can control. I buy mine from Stencils Unlimited. I've tried the Pololu stencil but it didn't work at all for my small parts (down to ~0.2x0.4mm pads and 0.4mm spacing between pads). I use Kester leaded solder for the stenciling and zephpaste for any rework/extra.
For stenciling I setup a system using a large piece of MDF as the base. To attach the stencil I tape it to a row of extra PCBs to make a hinge. Underneath the stencil the board is kept in place by a few more boards taped to the MDF. This allows me to stencil multiple boards in a row. For each board I'd have to fine tune the alignment and use my extra hand to stop the stencil from shifting while depositing the paste.
The scotch tape isn't very reliable for alignment, so for my next run I'm going to use a router to cut pockets for the PCB in the MDF then a pair of toggle clamps to hold the stencil edge in place. With this system I hope to be able to stencil multiple boards without worrying about alignment.
A TQFP48 would be the fine pitch small package solution for Prop, but the die is too large to fit...
I've just seen a even-worse QFN, which is a QFN16, with 4 square pads added to the corners to make QFN20.
Here are photos of the rough frames I use in house. The first one is mounted on a plastic base. The white plastic angle with the notch in the corner came with a SS stencil that I bought a long time ago from 4PCB. It is 0.062" thick and originally came with a similar plastic piece to hold the opposite corner of the PCB. But I lost that. No matter, I just make an arrangement of other PCBs to frame in the opposite side of the board, and everything is taped down securely with vinyl electrical tape. The stencil is held on the top edge with electrical tape, after careful alignment under binocular goggles. Then it can take one board after another, snap into alignment. The notch in the corner is important to help get a grip on the finished board. The staco clamp isn't such a good idea, I think, because it would put stress at one point and allow stretch and rotation. I have a similar arrangement for 0.031" boards made completely of old PCB material.
To stencil the boards I've made my own "frame" out of MDF and two toggle clamps. I had the stencil made by Stencils Unlimited, and it has both the top and the bottom of the board on one foil.
I cut a two level pocket in the MDF with a router. The shallow pocket is cut to a depth equal to the thickness of the PCB. This allows for the stencil to sit flat when in the down position. The deeper pocket is to fit the bottom layer components when stenciling the top layer. When stenciling the top layer the board sits on the large side tabs over the pocket.
To keep the board in place I have 4 small scrap PCBs held in place with double sided tape.
To position the stencil I put a board into the holder and put the stencil on top. I then slide the stencil until the apertures line up with the pads, and use the toggle clamps to hold it in place. I haven't experienced any problems with the clamps distorting or otherwise damaging the stencil. It seems that the thickness and stiffness of the MDF helps, along with the rubber feet of the clamps. There are also no issues with bending the stencil foil and using the clamp axis as a hinge.
Since there is only one pocket I have to re position the stencil when switching board sides.
I can then stencil normally, and do several boards in a row if need be. The most that I've done at once is 6, and I didn't have any problems with the stencil slipping. All the parts got perfect stenciling, even the tiny 28 pin part with 0.4mm pad center spacing.
The main improvement that I would work on is a second pocket so that I don't have to reposition the stencil to switch sides.
I should also point out that I haven't had any issues soldering the QFN Propeller chip (100% success so far). Much more challenging is the 28 pin part with 0.4mm spacing. I've discovered that component must have perfect placement the first time, otherwise rework success is very low (<25% so far).
I'm impressed. Thanks for sharing your setup. I'm just getting started doing this kind of stuff (though in a minor league).
I think your tips will be very helpful.